Hurricane season is almost over, and we’re excited to start sailing again. Before doing so, however, we had one important task to complete in Grenada — getting a haul-out for our boat. For those of you who aren’t boaters, you may be wondering, “What is a haul-out?” It is a nautical term for hoisting a vessel out of the water and onto land using a travel lift, for the purposes of inspection, cleaning, maintenance, repairs, and storage. As a boat sits in water, the hull naturally accumulate growth, and conventional wisdom says it’s best to haul out annually to clean the bottom. Most cruisers haul out every 18 months to two years, but the better the hulls are kept up, the better the boat will perform. So we were eager to get Hope out of the water for some much needed TLC.
When we arrived in Grenada at the end of June, we went to Clark’s Court Marina on the southern side of Grenada to schedule our haul-out for Hope. This busy boatyard has a good reputation, so we weren’t surprised to find out that they were booked months in advance. We had to wait until Oct. 8th for our haul-out, but for us, that turned out to be the perfect time to get the work done, right at the end of the hurricane “waiting” season, and right before we started sailing again!
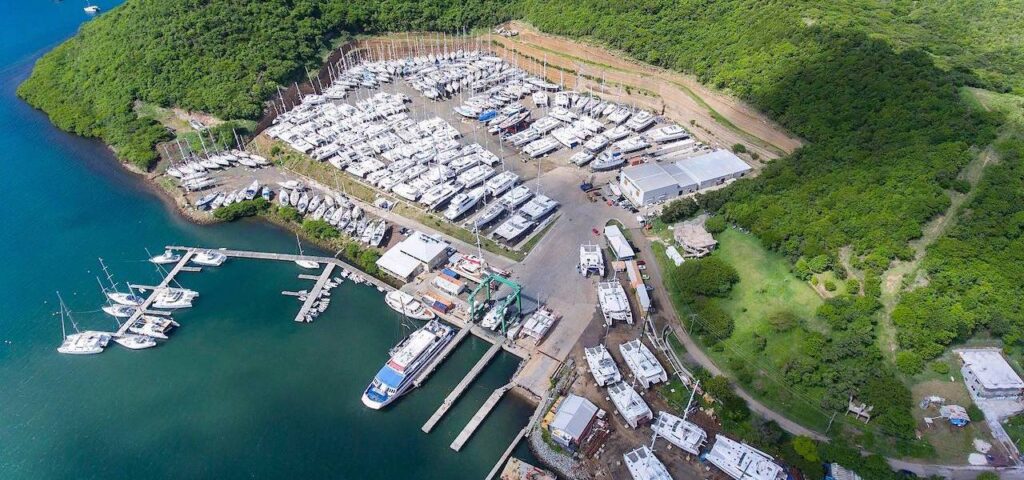
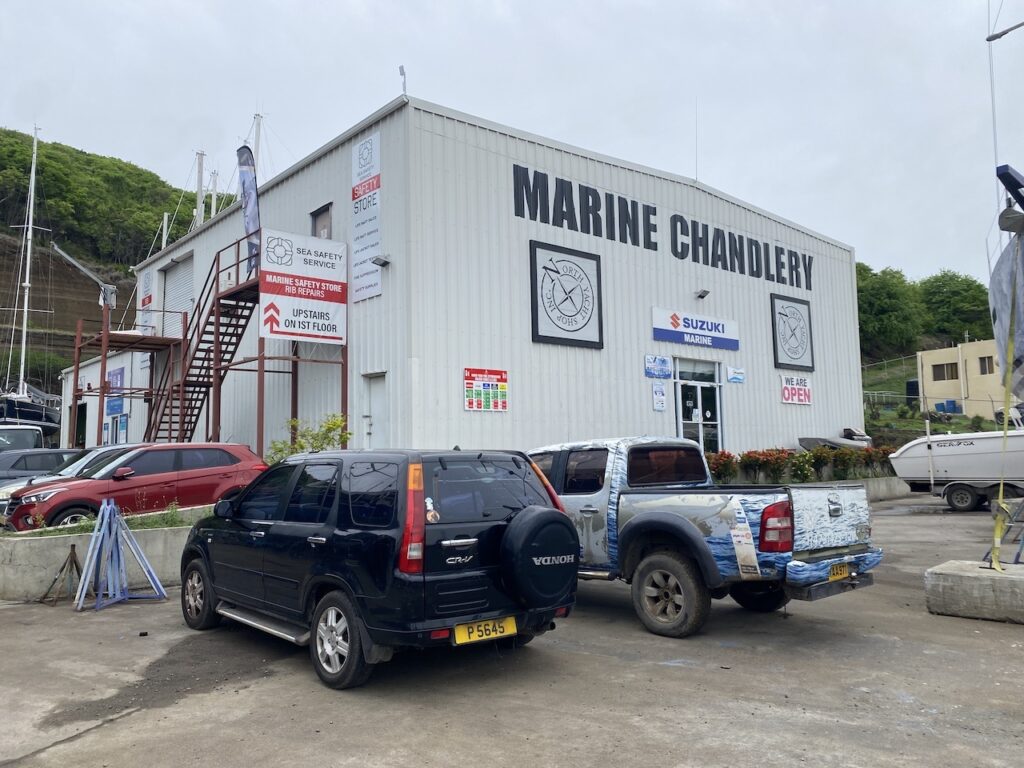
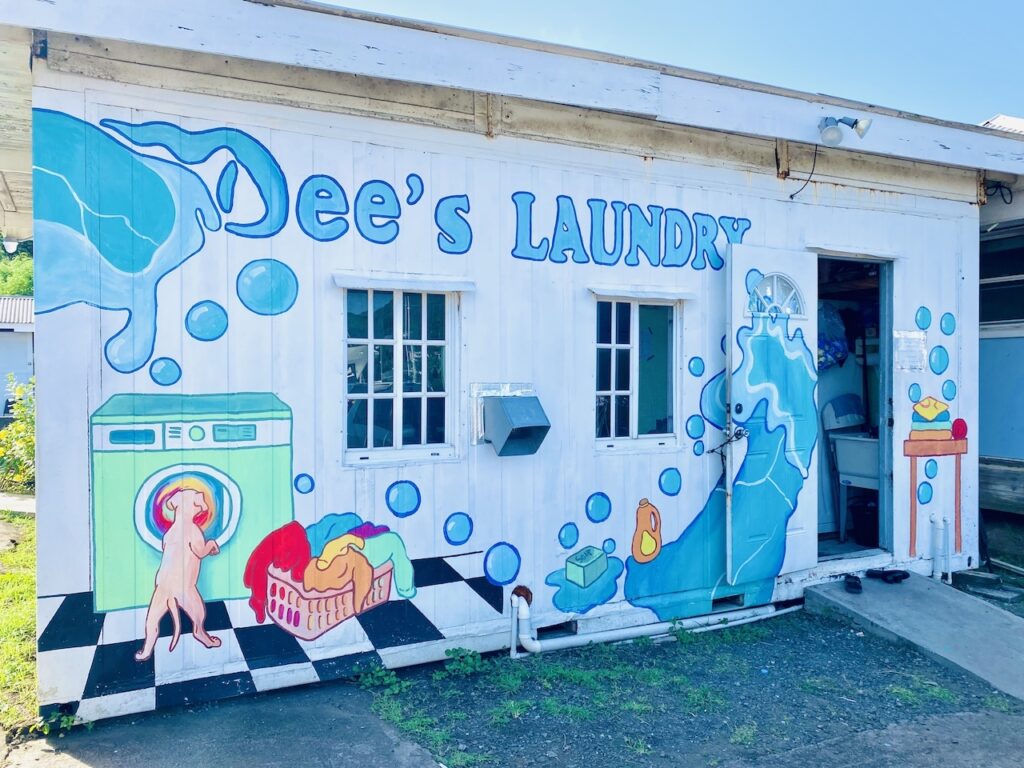
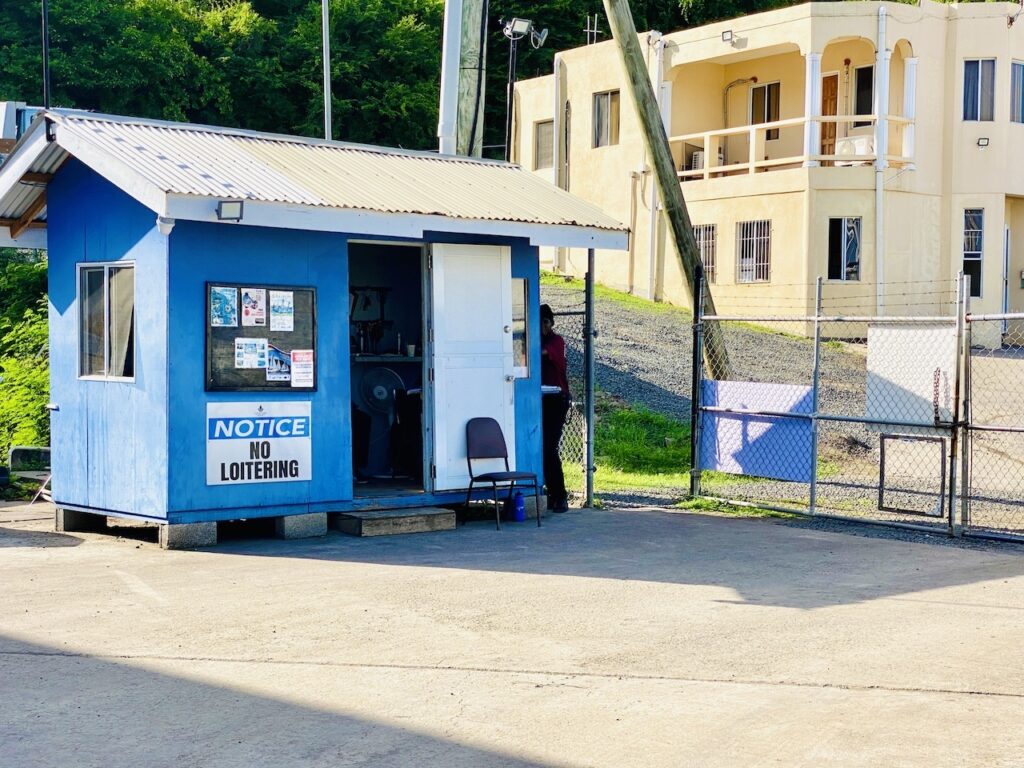
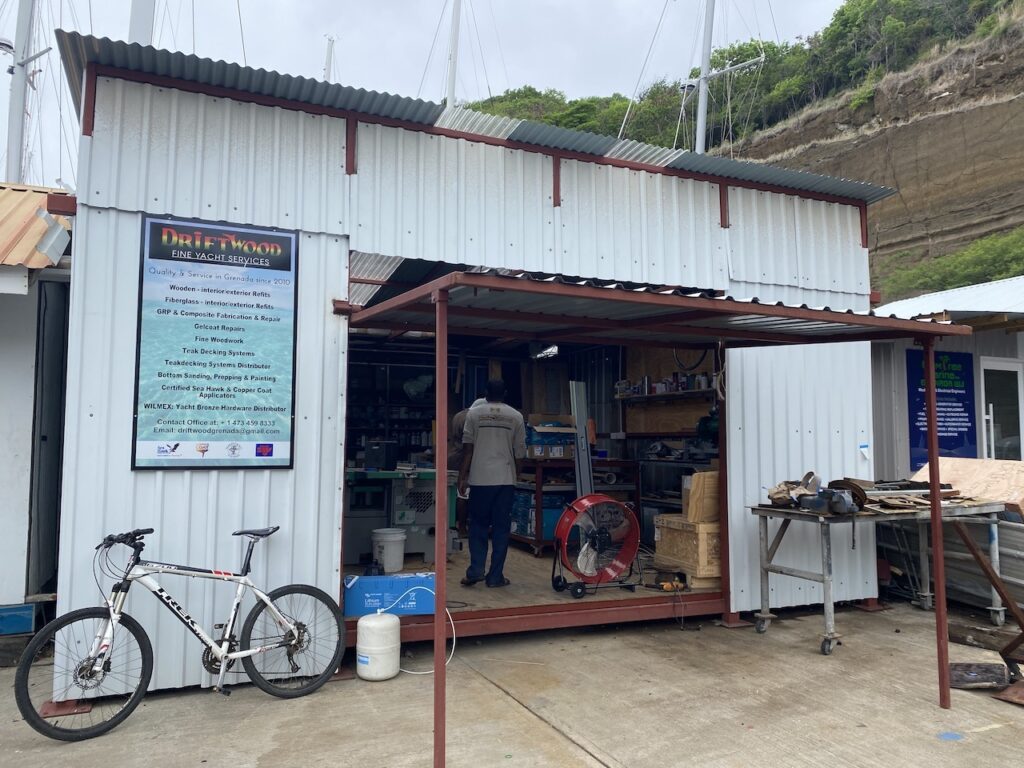
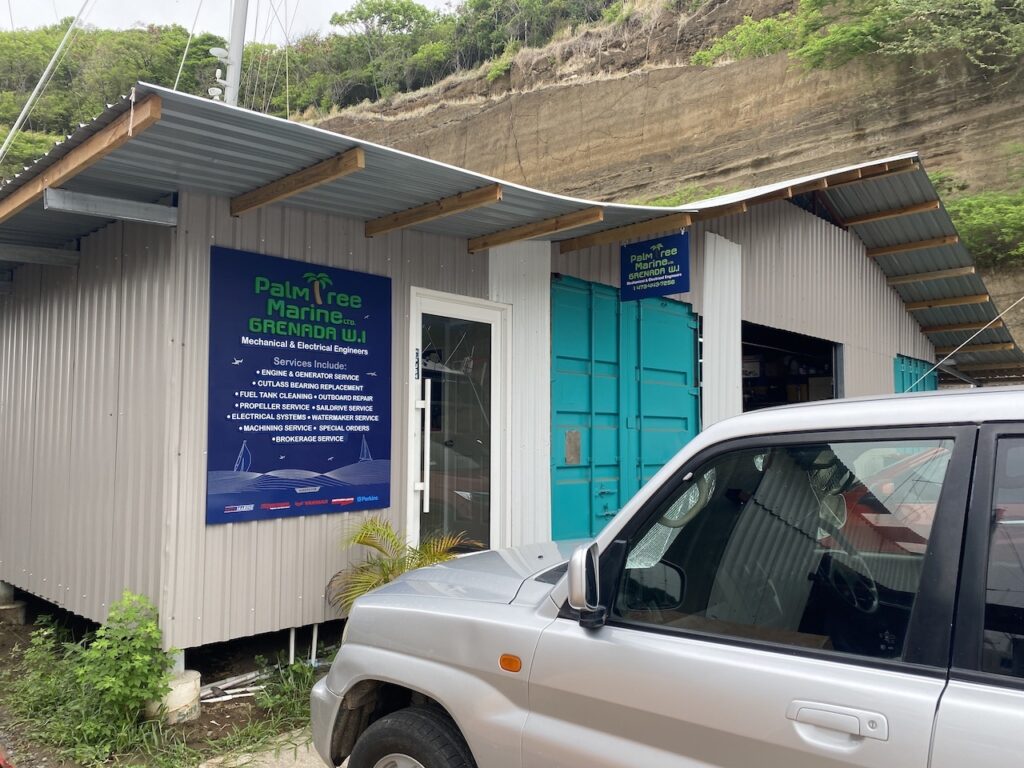
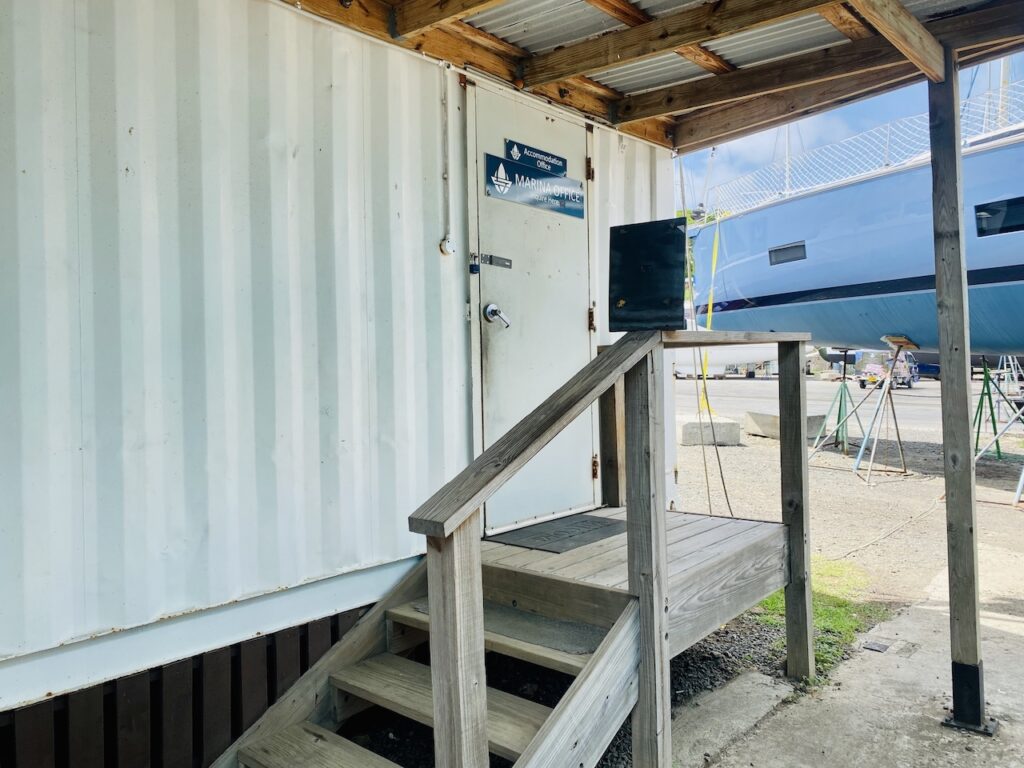

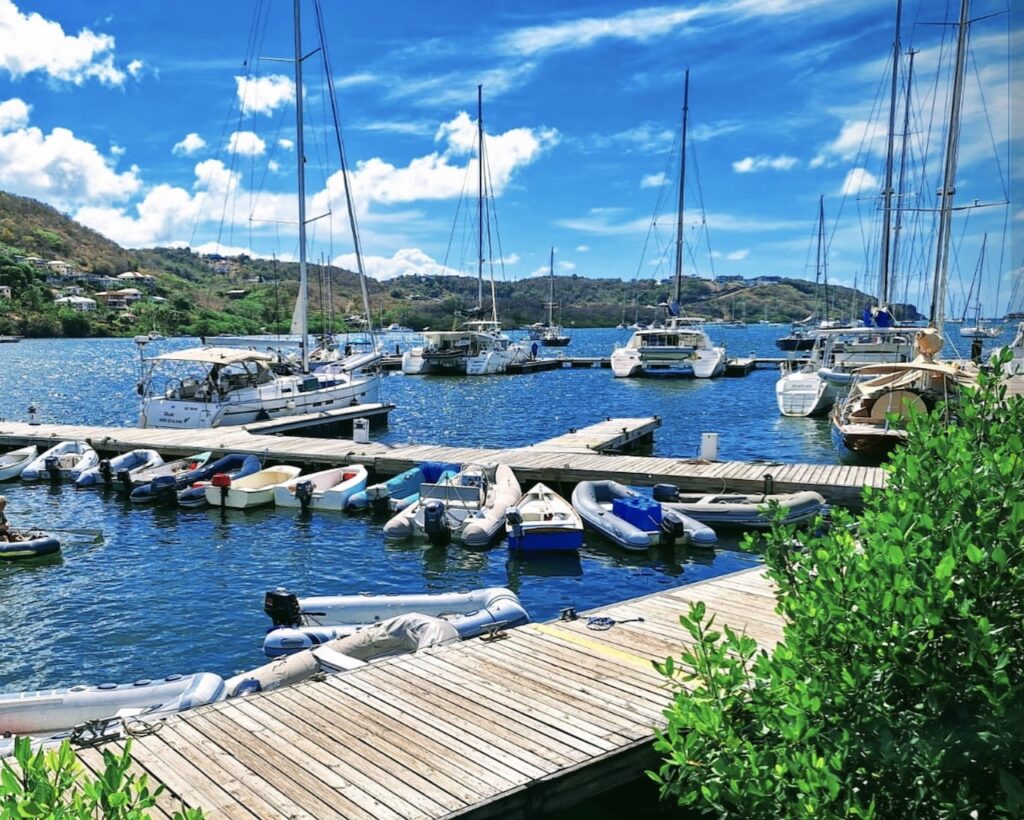
We had a lot of preparations to do before our haul-out day. We began by removing all of the outside seat cushions and taking down the enclosures to prepare for a thorough boat cleaning. We stored the cushions and Isinglass in the port aft cabin. Then I removed all of the loose items from the exterior of the boat to make it as bare as possible for the the wash down and wax.
The marina requires all sails to be taken down before hailing vessels out. So Kory and I took down the Screecher and stowed it in one of our storage lockers. However, when it came to the task of taking down the mainsail and then putting it back up again, we decided it was a challenge we weren’t wanting to do at this time. Thus we opted to hire out the job.
We got on a dock at Spice Island Marina for a couple of nights while Turbulence Rigging & Electrical boarded the boat and removed the head sail (Genoa) and the main sail (including the StackPack). After seeing how much work it was to get the main sail down, remove all of the battens, jacklines, and cover, then fold it, and lift it off the boat, I’m so glad we hired others to do this job. The price was reasonable and it saved our backs in the process. While the boat was hauled out at Clark’s Court boatyard, Turbulence Rigging had time to inspect our sails, repair any rips or unraveling seams, and install new tale tells. Our sails hadn’t had this kind of inspection and service since buying the boat almost two years ago, so it was time.
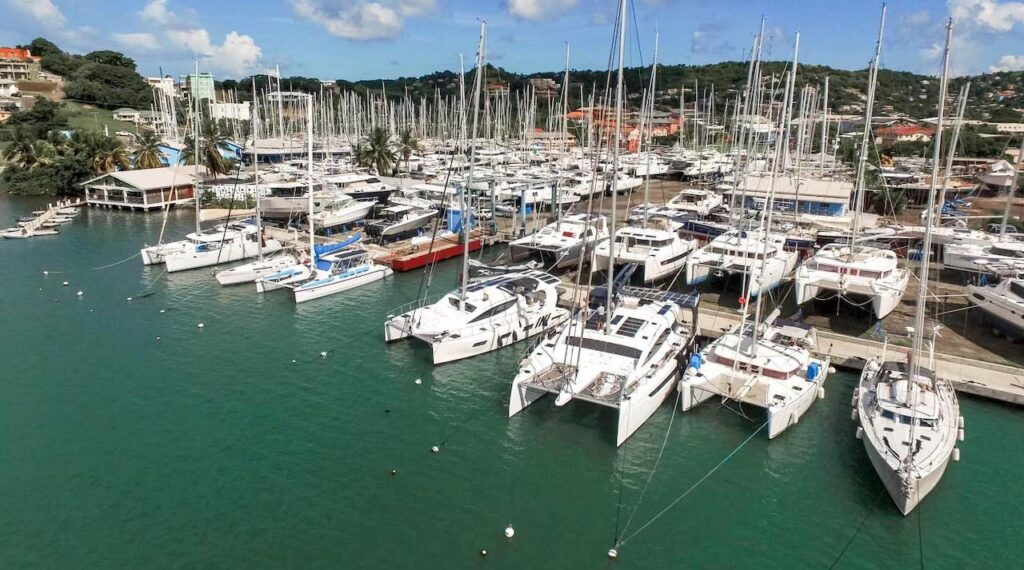
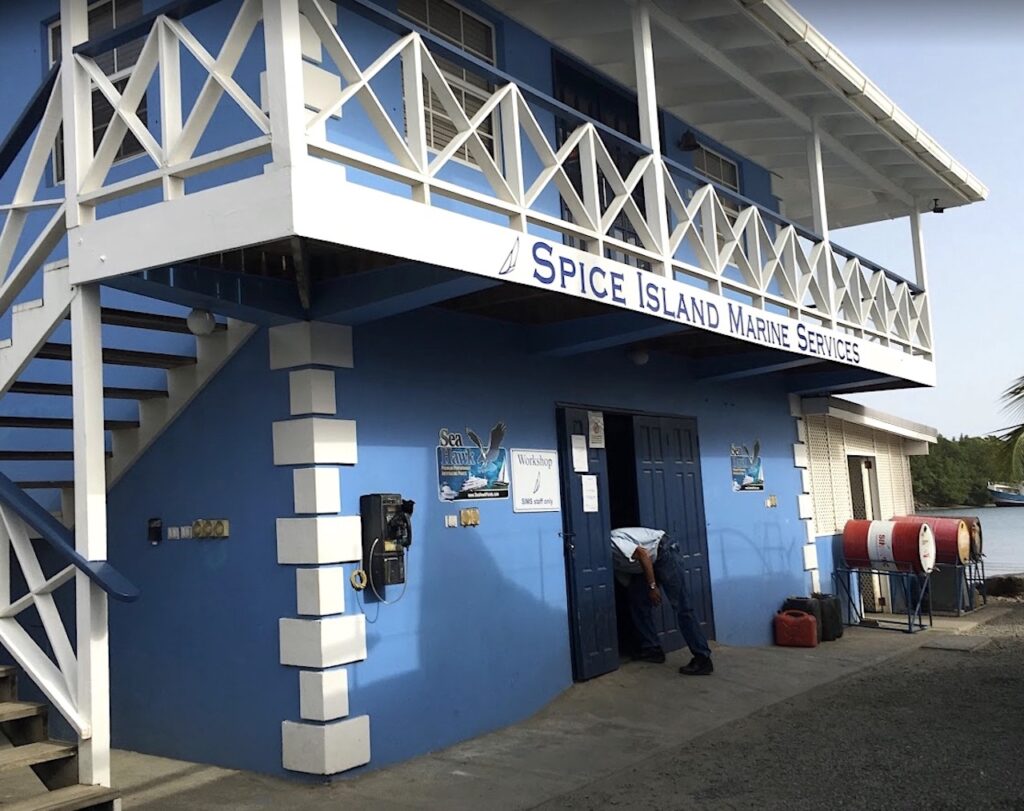
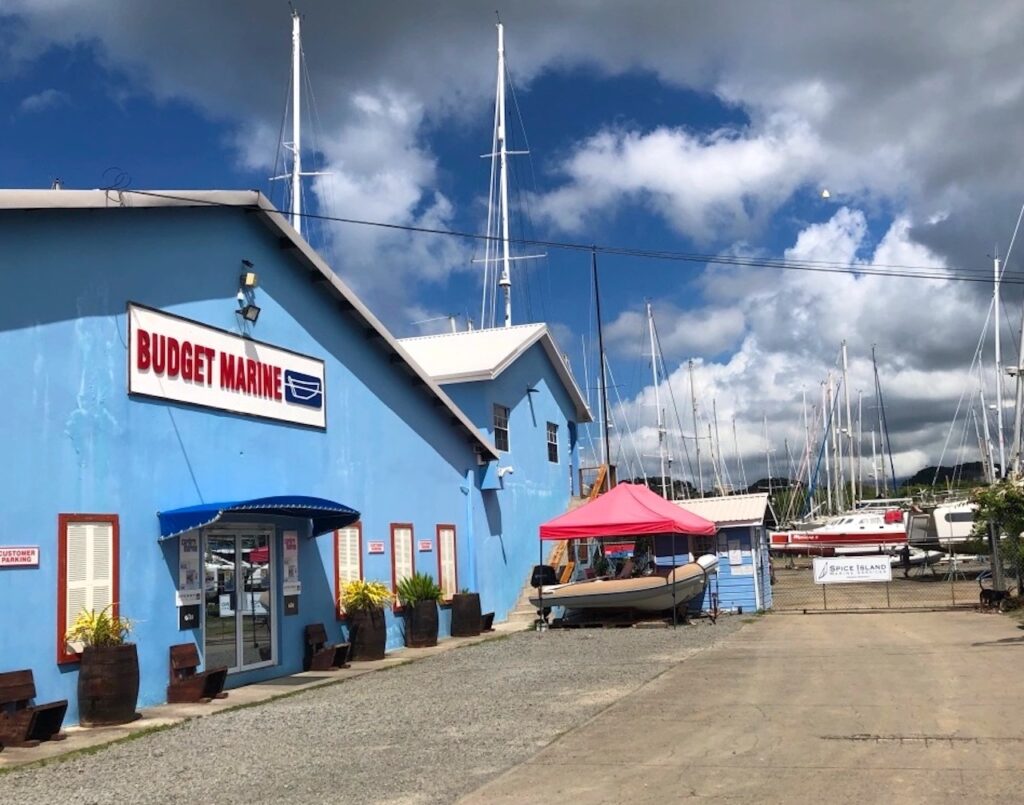
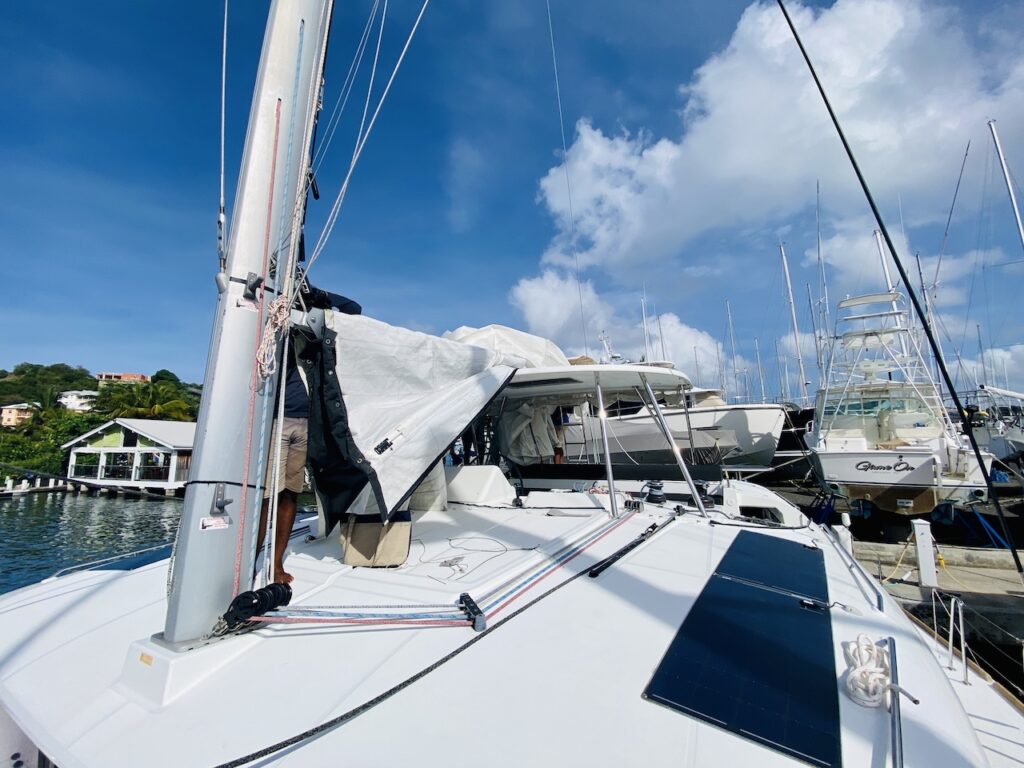
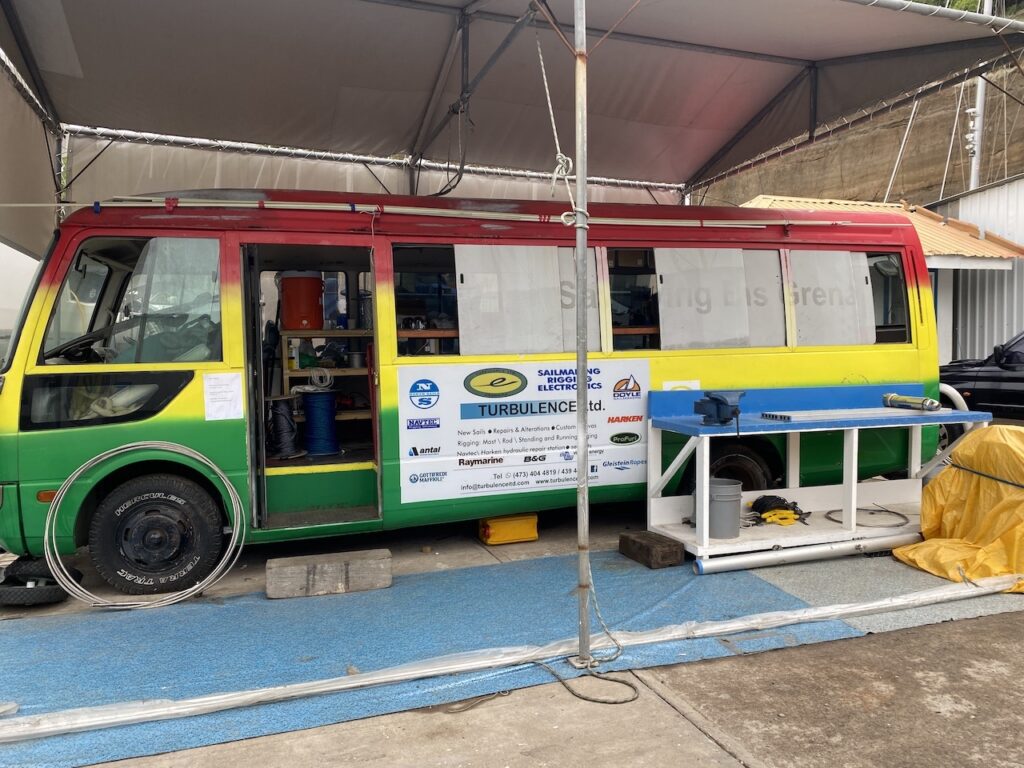
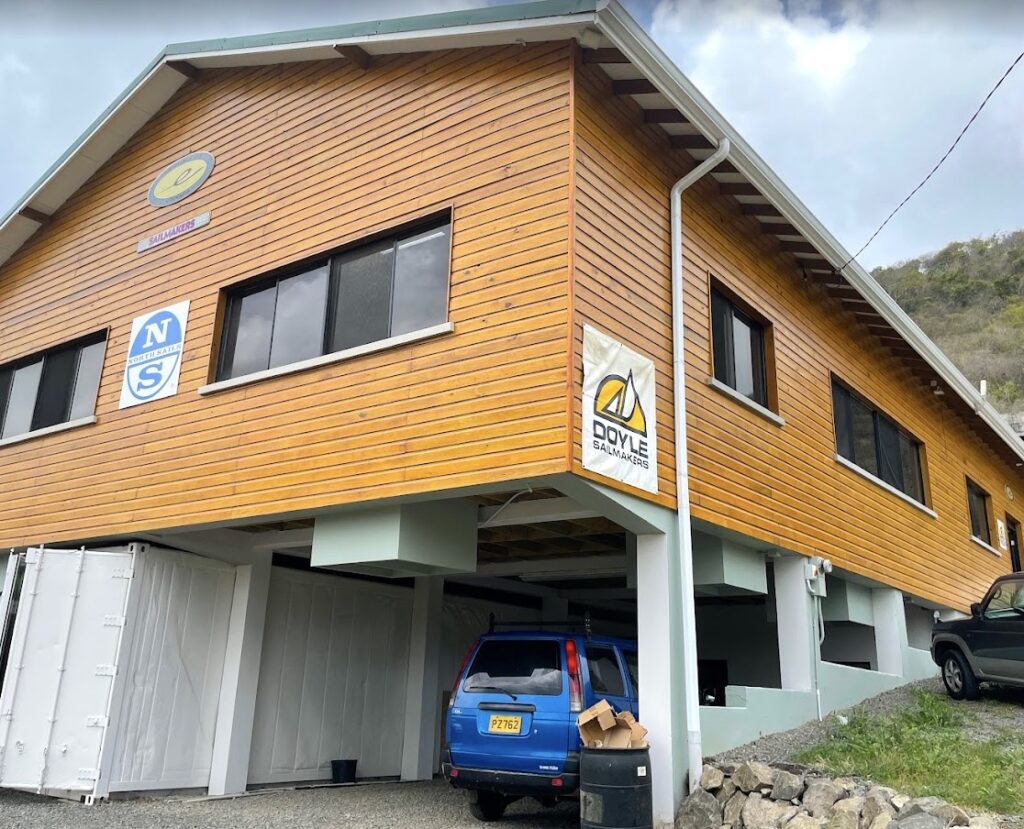
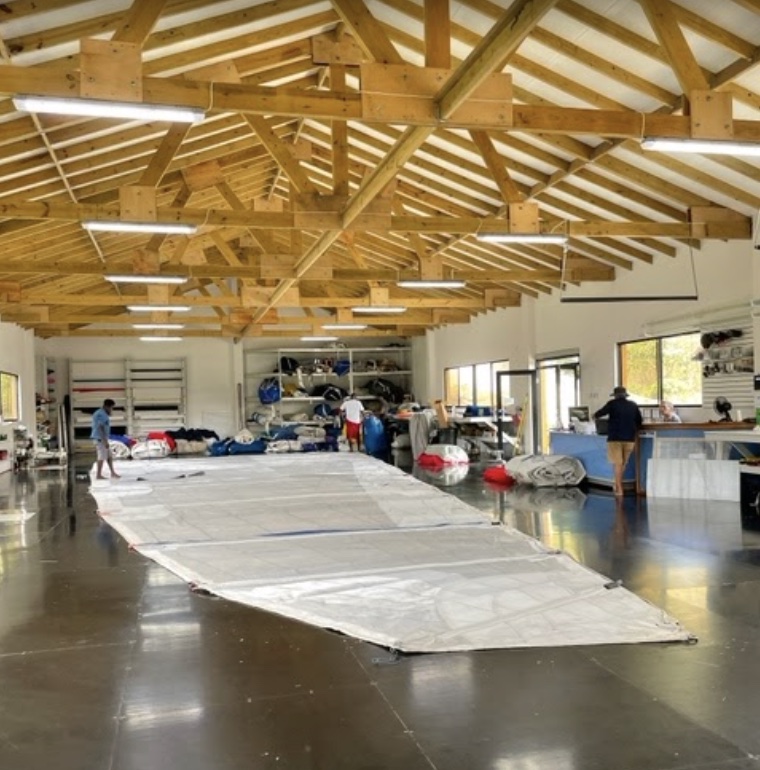
We also prepared for the haul-out by pickling our water maker. This is a process that involves filling the system with a sodium bicarbonate solution to prevent microorganisms from growing and damaging the membranes. If we were only going to be out of the water for a week, this probably wouldn’t be necessary. But since the boat was going to be sitting in the hot, humid boatyard, with stagnant water in the water maker for at least two weeks, we opted to pickle it to be on the safe side. It wasn’t a complicated or a time-consuming job, it just required Kory to fit in a hot, tight space, and then carefully pour in the solution without spilling it. The worse part of this task for me was having to remove all of the bedding to get under the bed and then remake it. A 15-minute job of pickling the water maker creates an hour-long housekeeping job, but that’s part of boat life!
Since we were on the dock at Spice Island Marina for three nights, plugged into shore power, we gratefully got to enjoy air conditioning full time. I took advantage of the AC by thoroughly cleaning the salon, master cabin, and heads. I can’t tell you how nice it is to be able to clean without dripping with sweat. I also took advantage of the unlimited water supply by washing all of the bed linens, rugs, towels, and salon pillow covers. While I was doing all of this, Kory was taking down the enclosures, doing some minor repairs, and organizing boat supplies.
After all of this work, we felt well prepared for the big haul-out day. We had two things left to do before we headed to Woburn Bay to go to Clark’s Court Marina. We hung fenders on both the starboard and port sides, and secured dock lines at the bow and stern on both sides of the boat, per the marina’s instructions. Our friend, Javier, on catamaran Momentum, hopped onboard before the haul out to help us with the lines. His boat was scheduled to be hauled out the following week, so he wanted to learn the process and know what to expect. We were grateful for his help; and, in turn, Kory helped him on his haul-out day. That’s what friends are for!
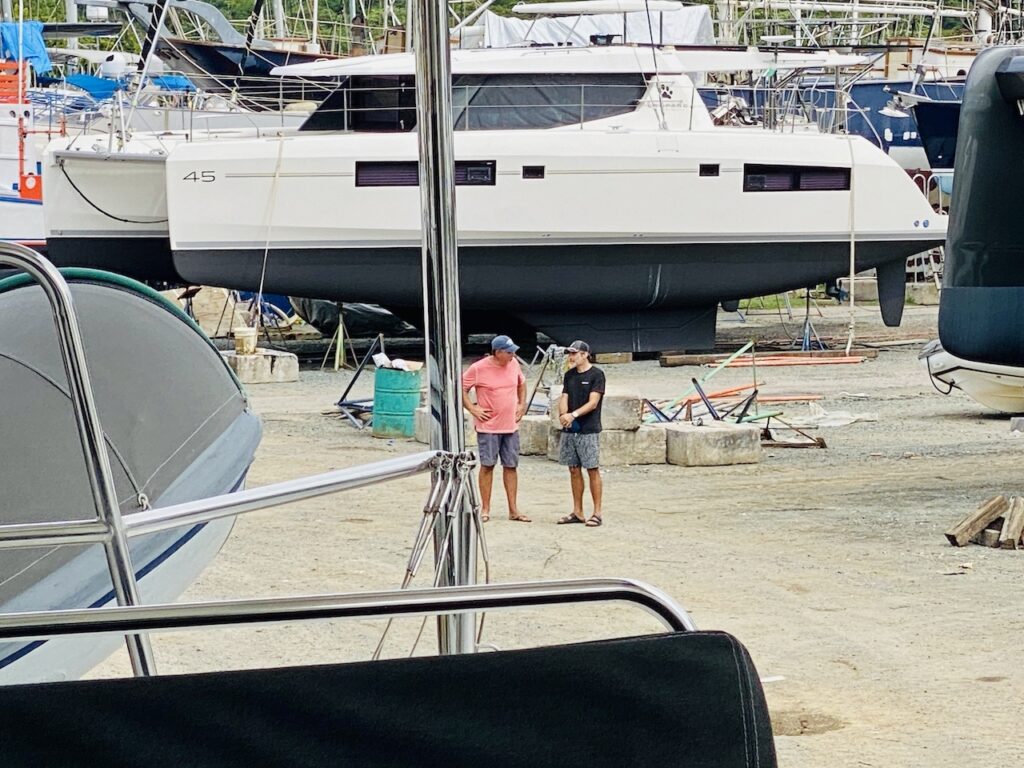
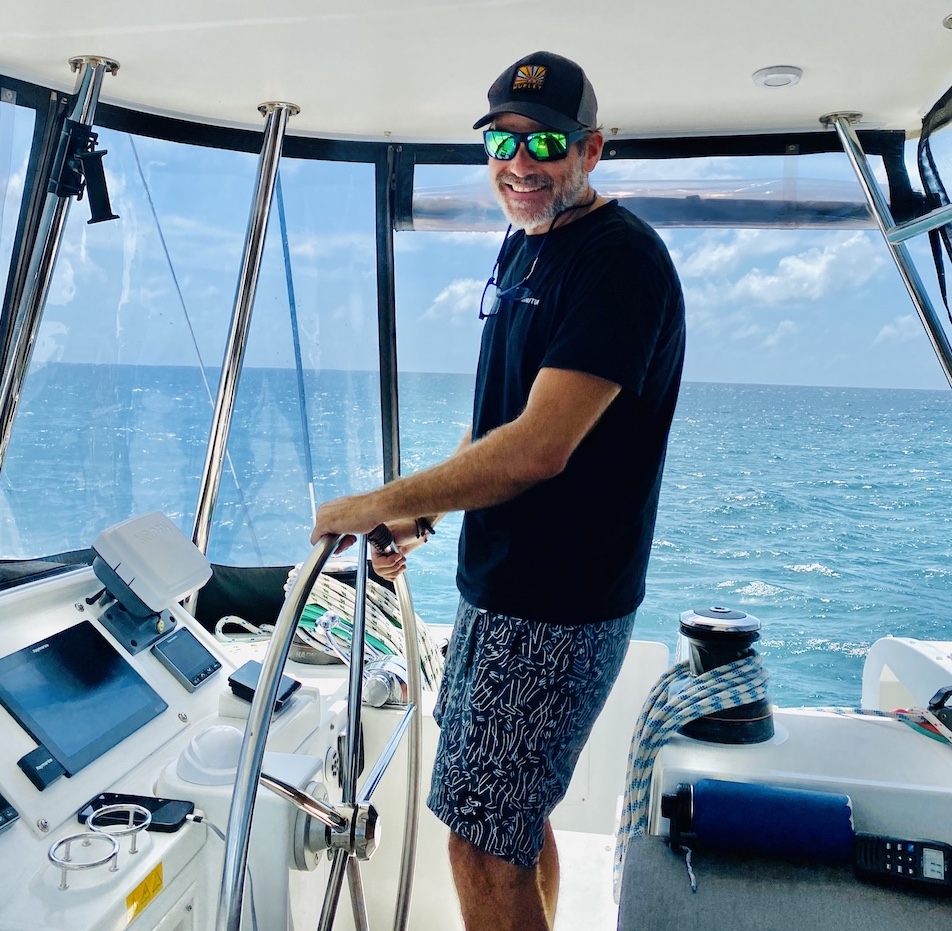
When we arrived at the marina, we had to tie up on a dock for about an hour before they could get us out of the water since they were using the boat lift to put another boat back in. When they told us it was time, we had all hands on deck to drive the boat into the boat launch, throw the dock lines to the dock hands, and wait for instructions. The wind was gusting to 20 knots and maneuvering the boat wasn’t east. But Kory is a great captain and made it look effortless as he drove us into the slip, while Javier and I threw the dock lines. After that, our work was done. We turned off the engines, locked the door, got off the boat with our necessities for the next two weeks, and watched the process as the workers hoisted our boat out of the water with a giant boat lift and set it into place on land. We were so thankful that everything went smoothly and that God answered our prayers for a successful haul out.
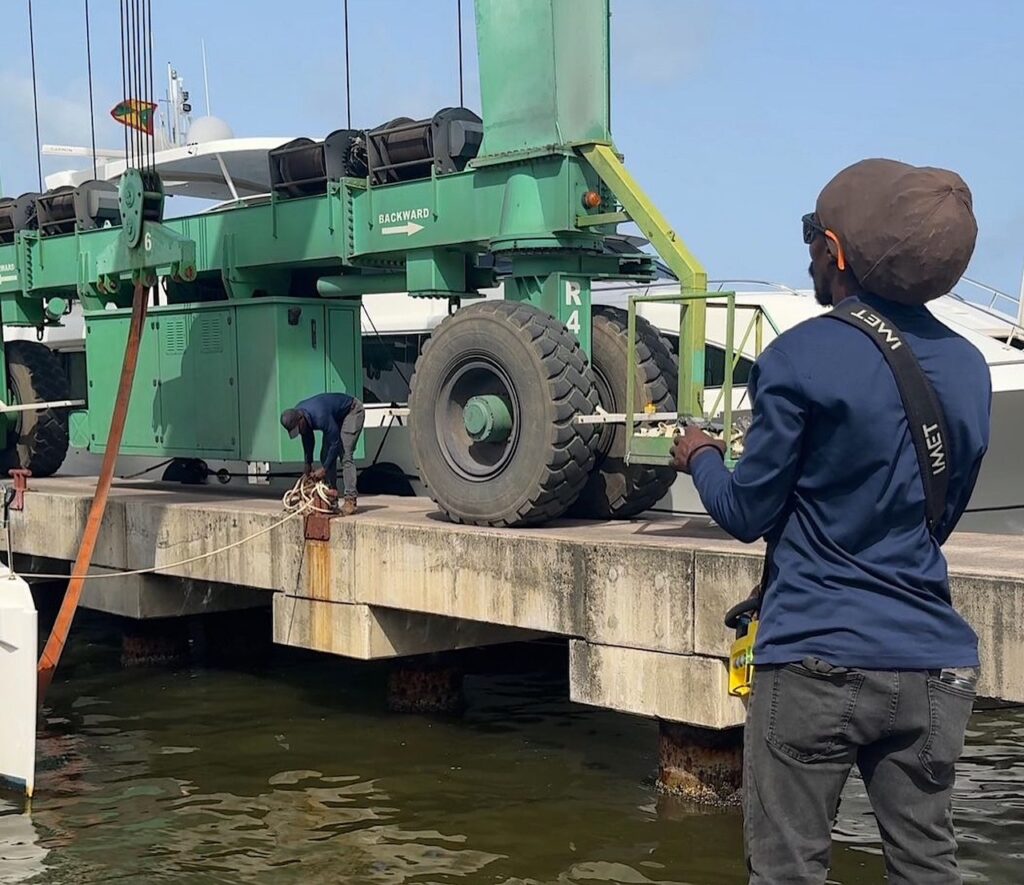
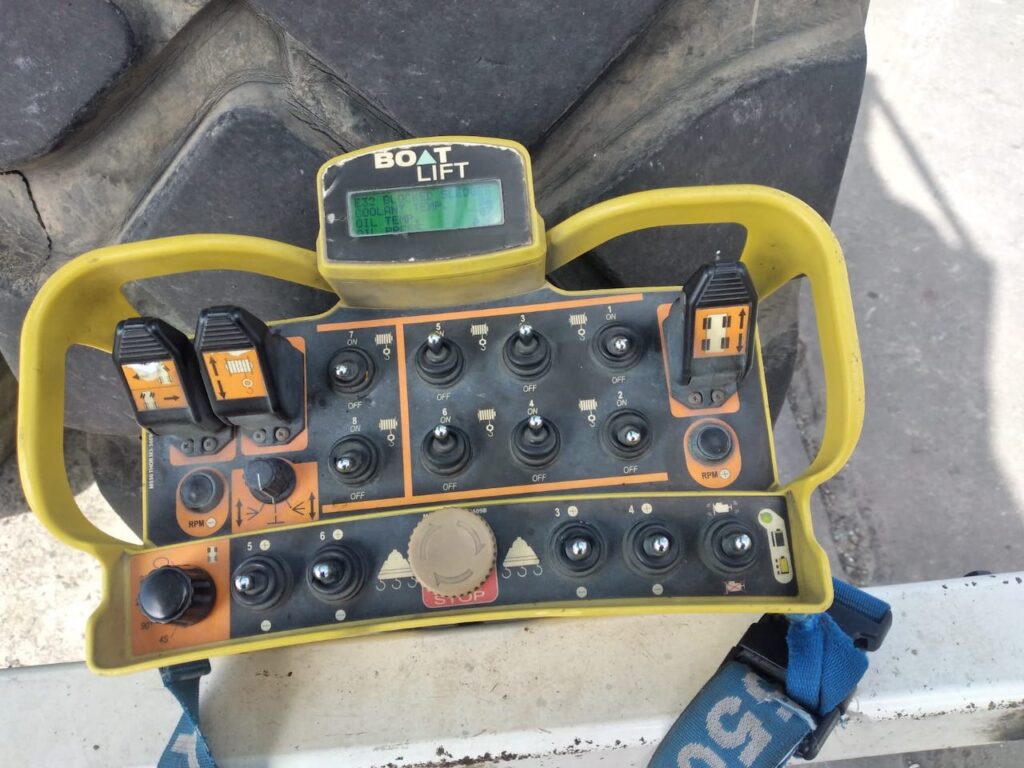
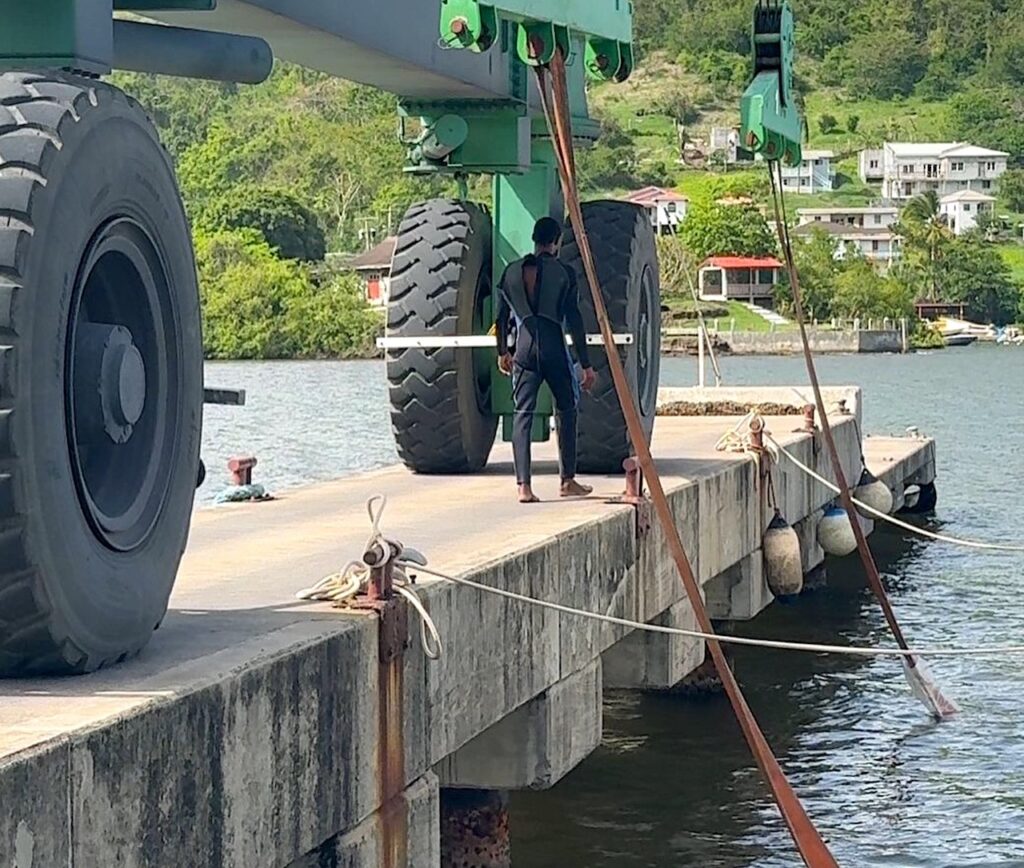
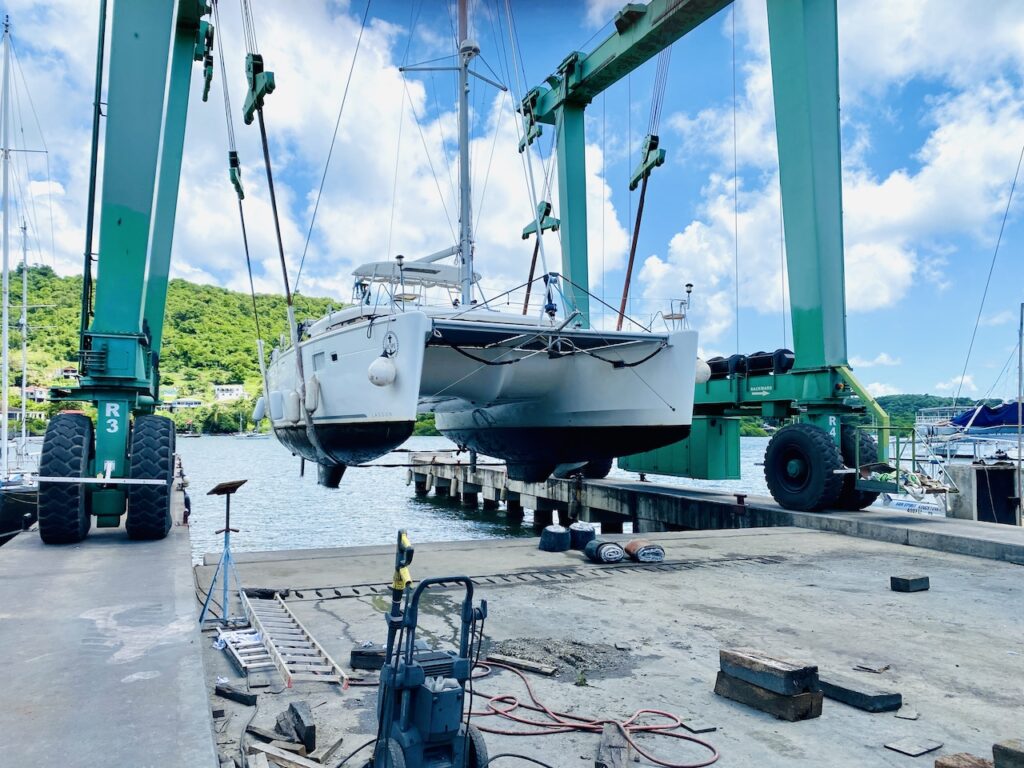
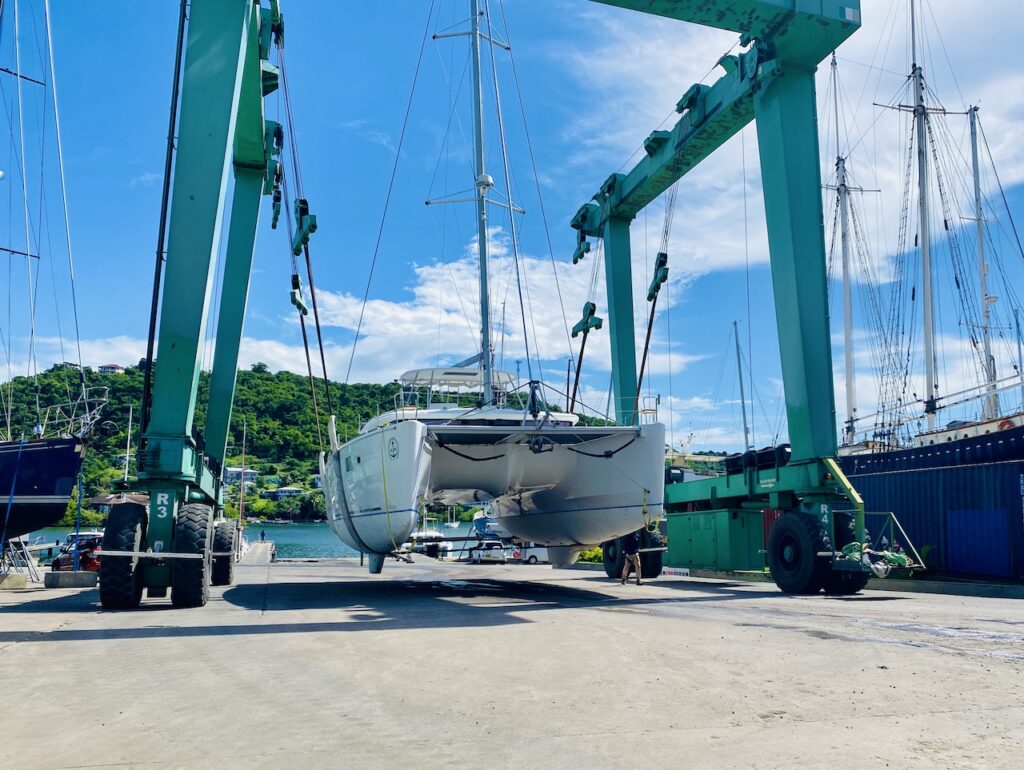
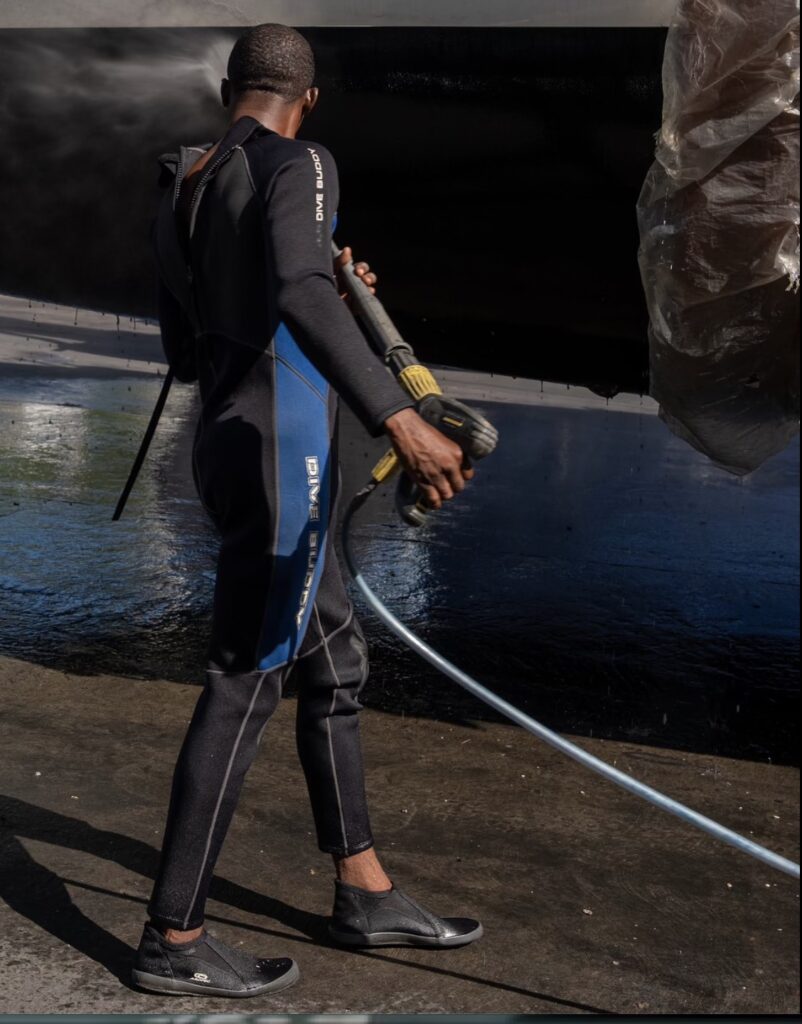
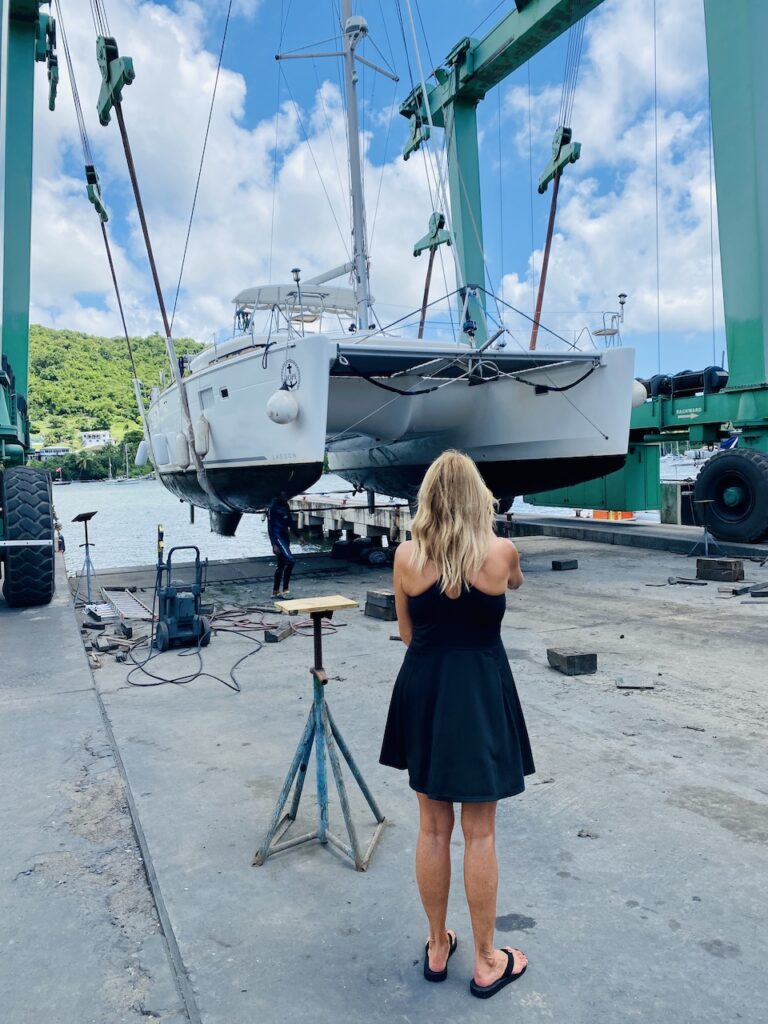
While our boat was on the hard getting work done, we stayed at the Royal Court Apartments, only a two-minute walk from the boatyard. It was definitely not a fancy place, but we chose to stay near the boat so we could monitor the work and also do some projects ourselves. Had we gone to a hotel farther away, it would have been difficult to stay on top of things and make sure the work was done correctly. We found this was a wise decision, as several of the workers needed either lessons on how to do things, or a push to actually work and not sit around liming (a Caribbean term for hanging out and shooting the breeze).
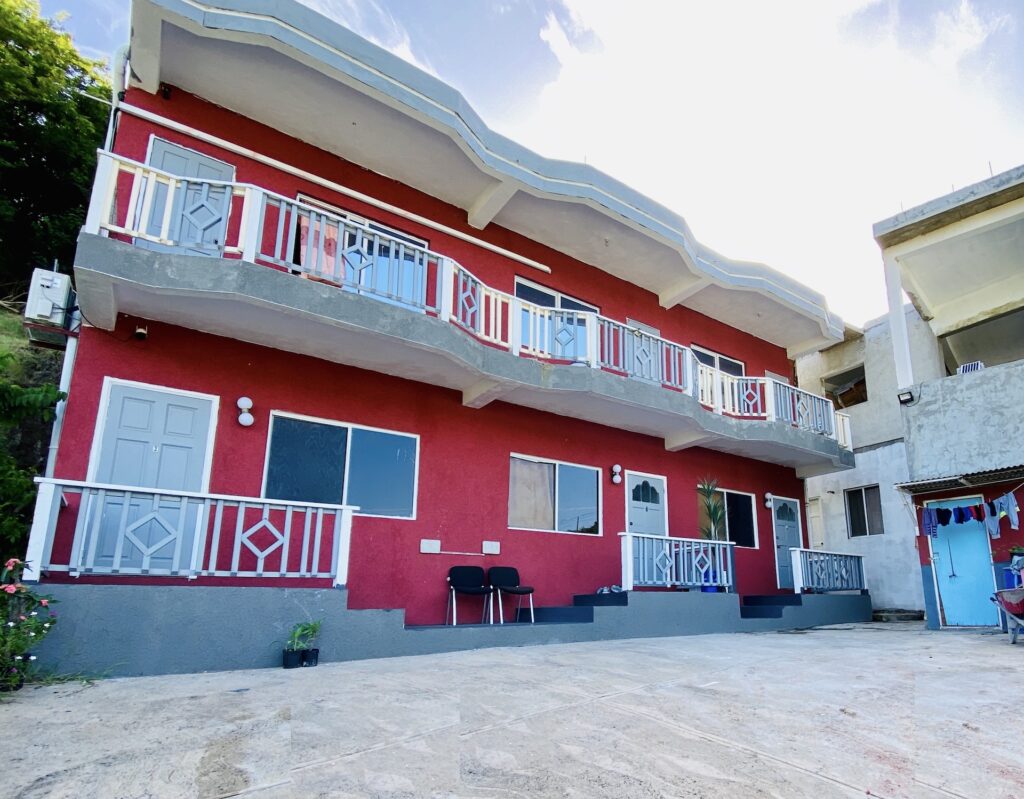
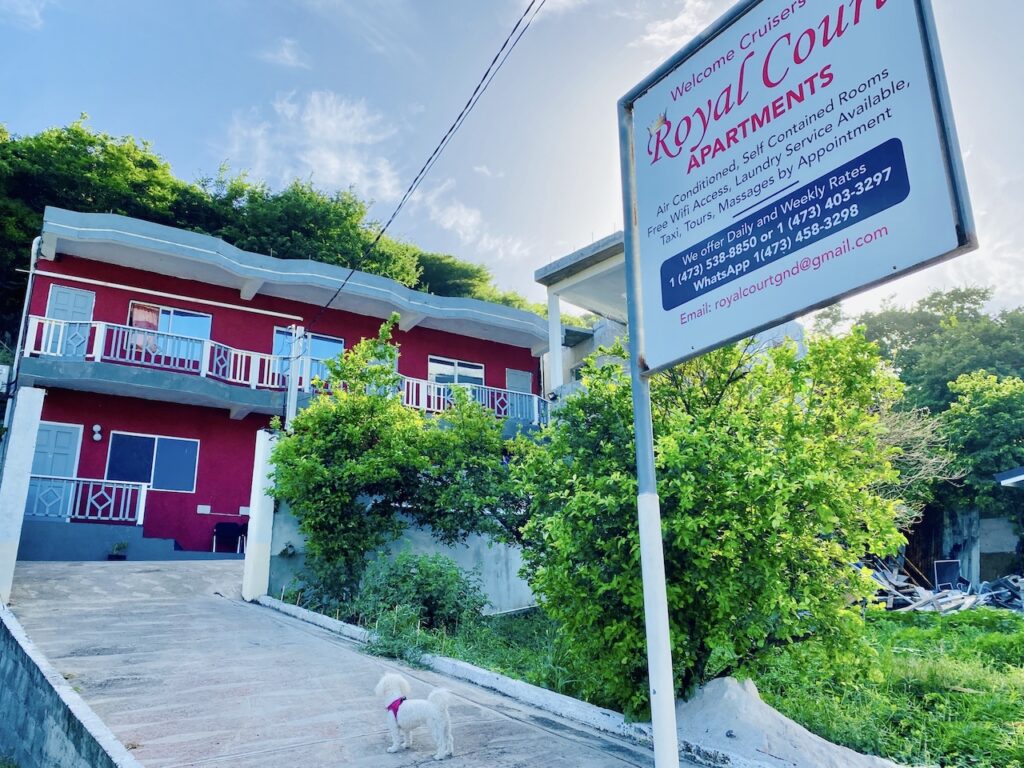
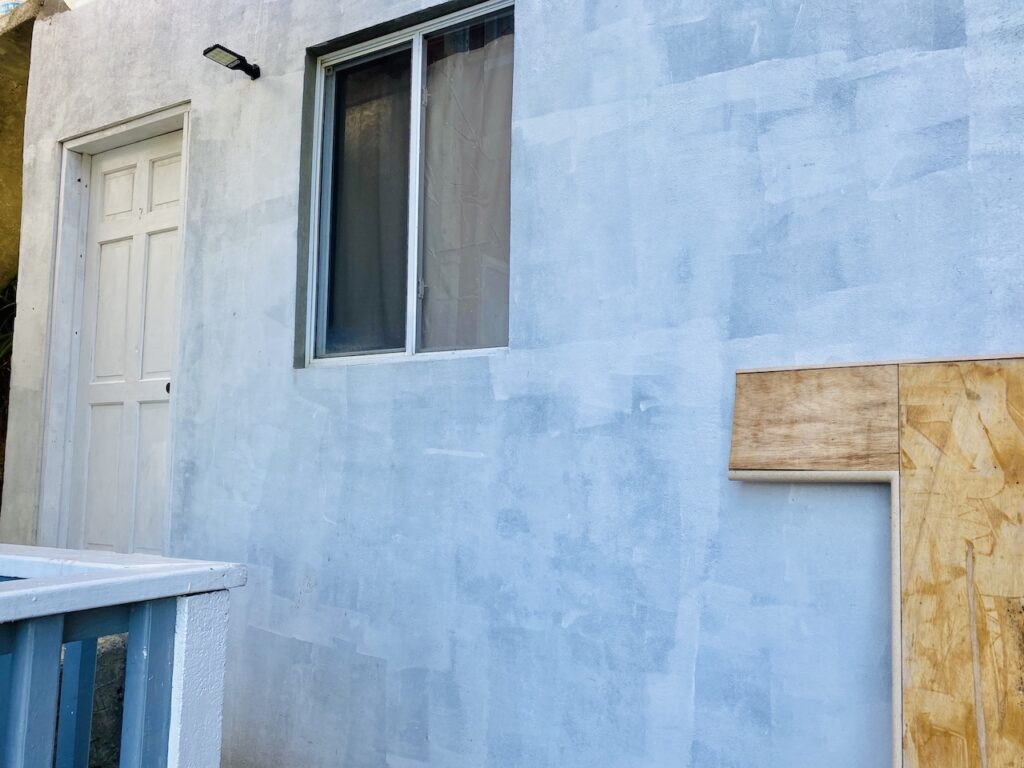
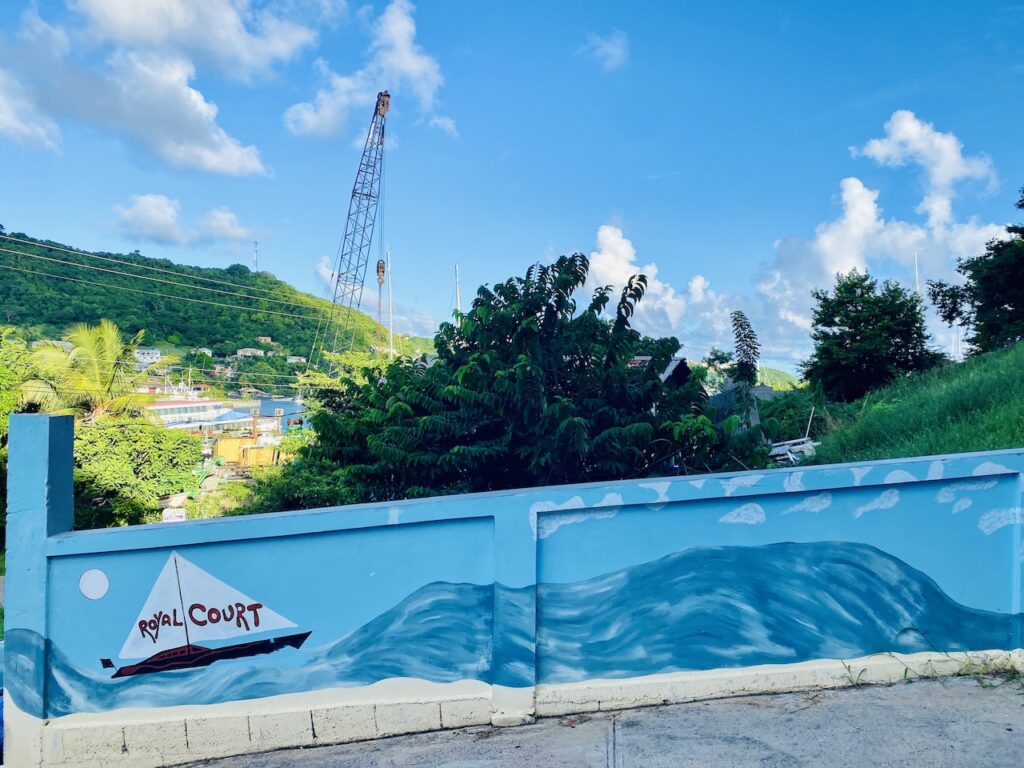
Our first night at the apartments was not a pleasant one. In fact, we strongly contemplated moving into a hotel the next day. The floors in our apartment were dirty and our feet were black by the end of the day, our bed was made up of two mattresses lying on the floor, the room had no mirrors, not even in the bathroom, and the toilet stopper didn’t work properly. The worst part of our first night was the giant cockroach I stepped on at 2am when I entered the restroom. I let out a scream and woke Kory to rescue me. He quickly discovered that there was a large hole behind the toilet that had never been sealed, and he could see two more cockroaches trying to make their way into the bathroom. This was turning into a nightmare, but we had nowhere else to go for the night. We left the light on in the bathroom (since roaches don’t like light) and closed the door so they would be contained. We longed for this night to be over.
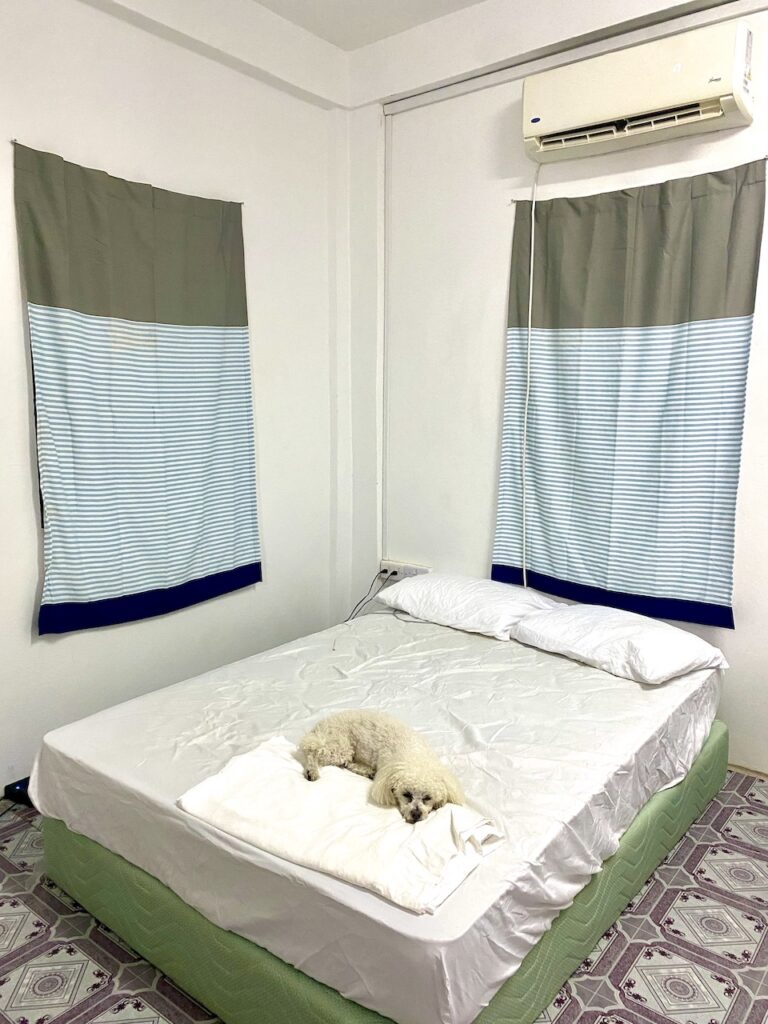
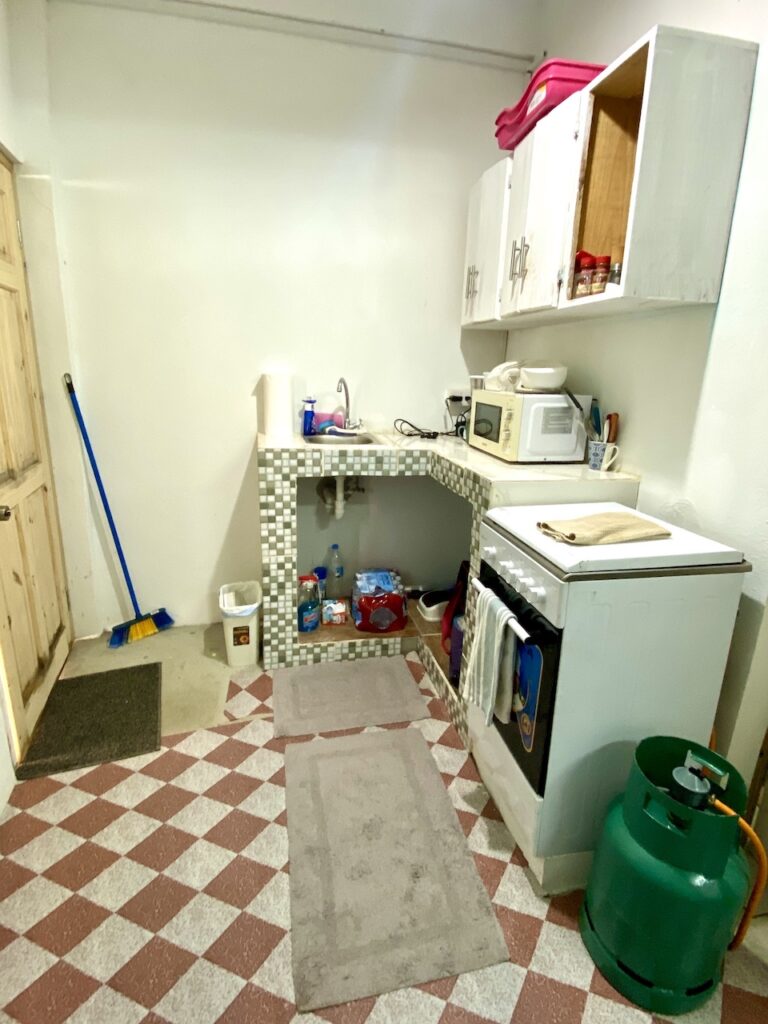
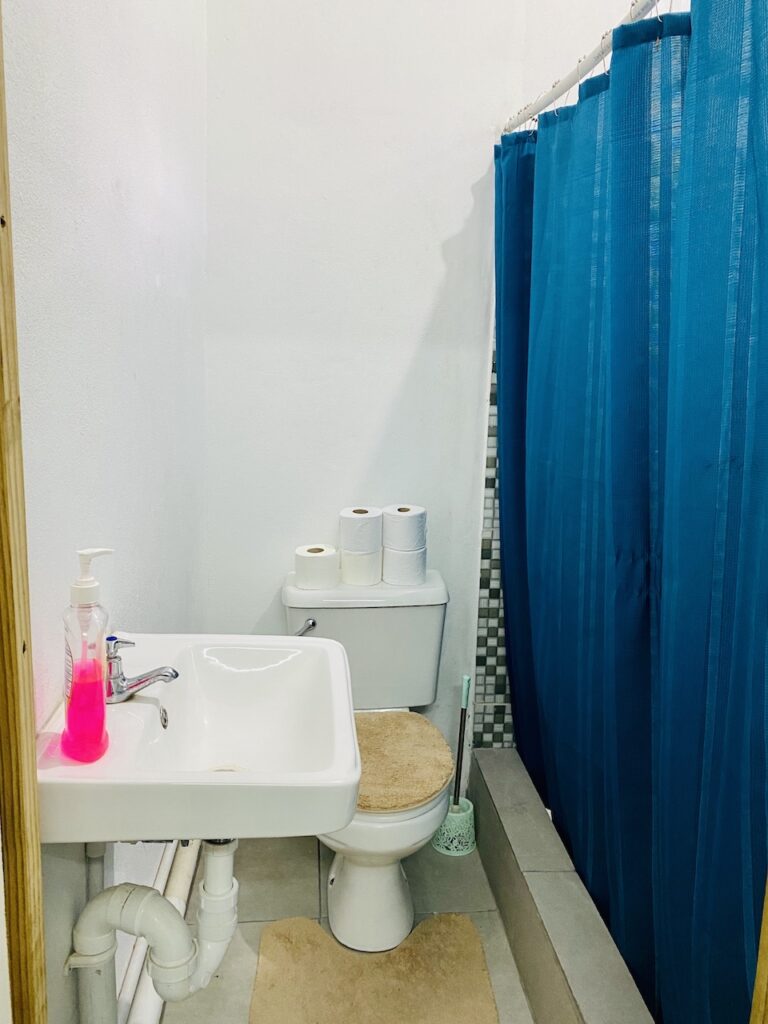
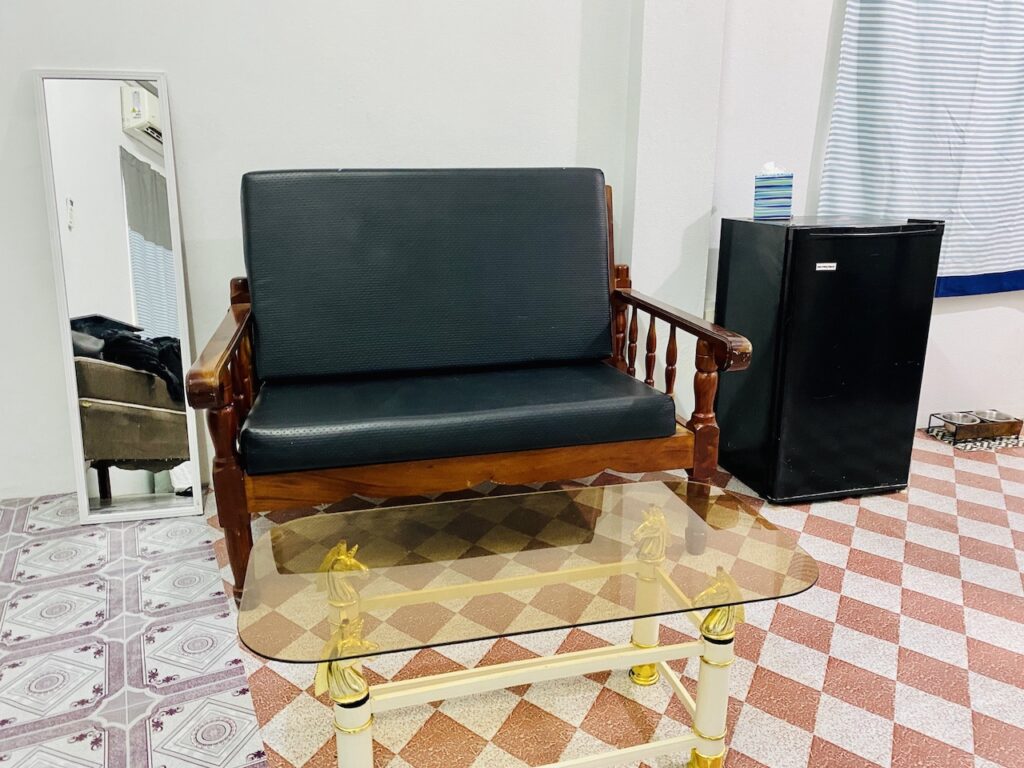
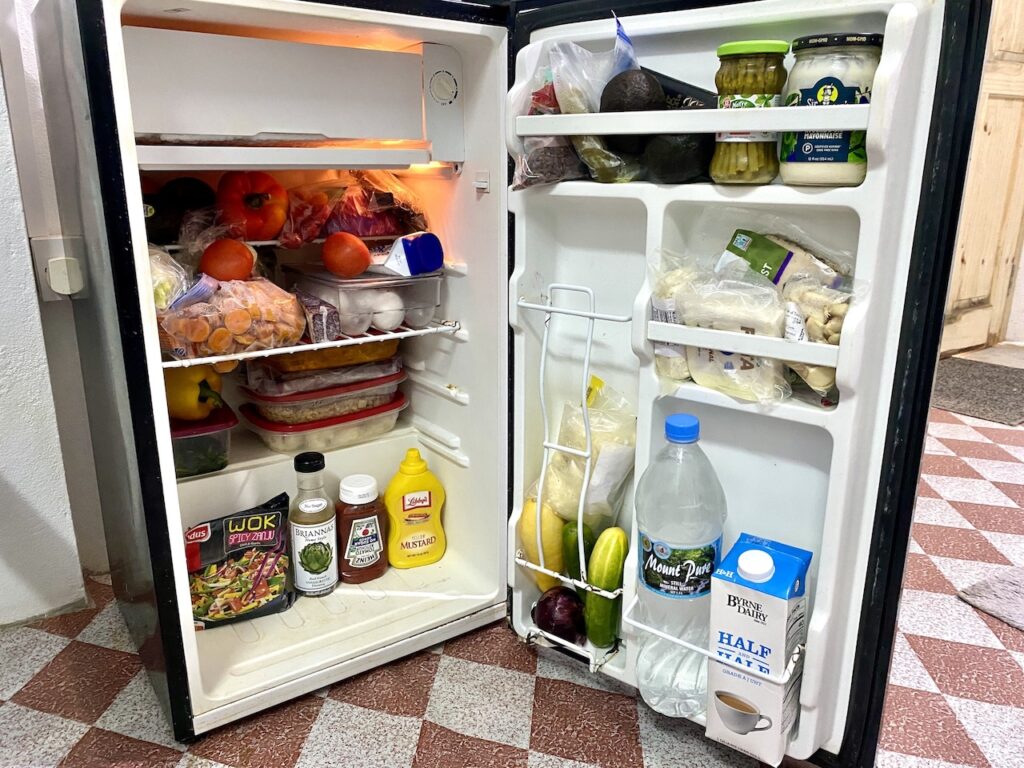
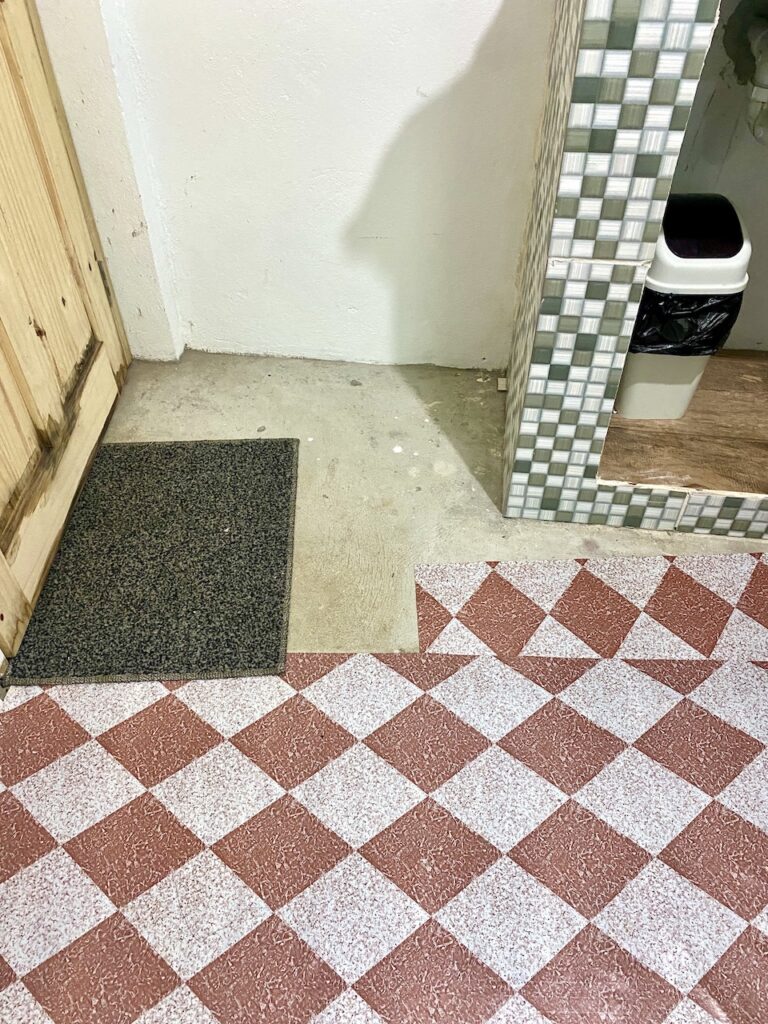
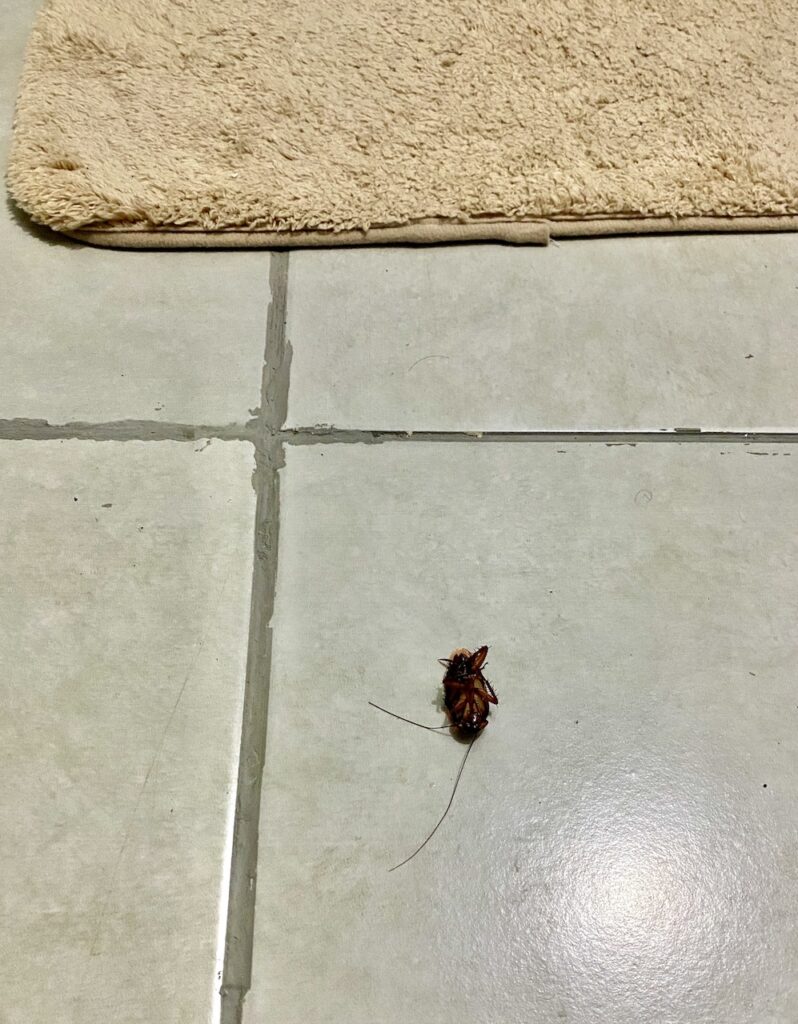
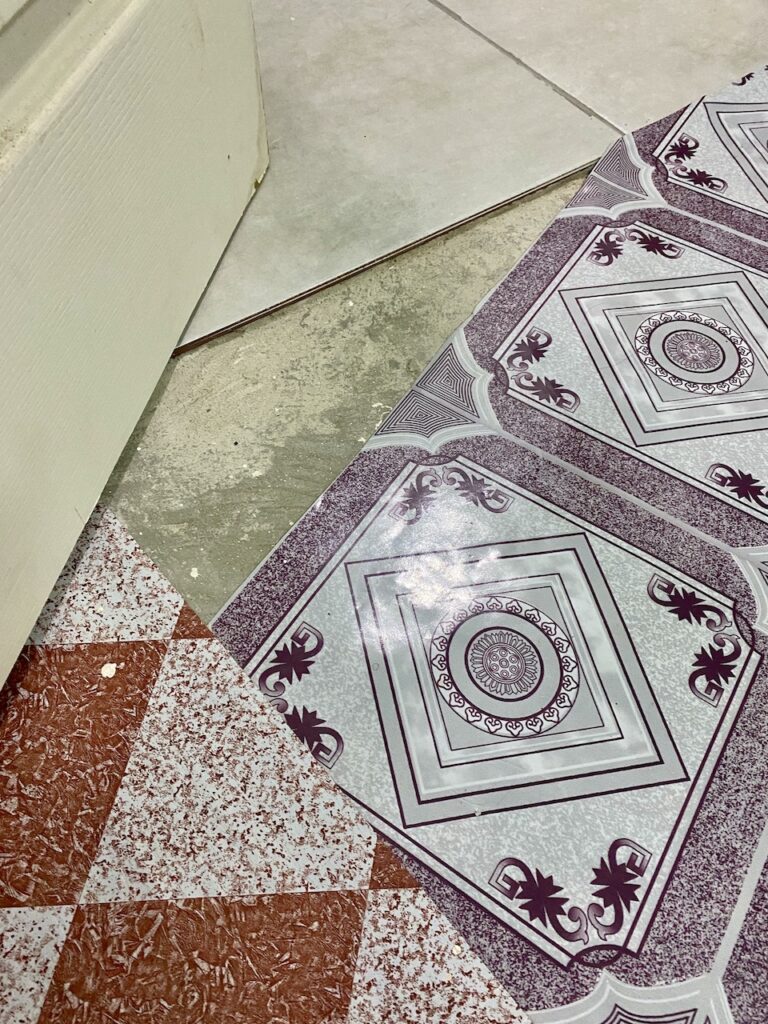
The next morning we discussed our options. Kory made some calls to a few hotels nearby with the intention of moving, but they were either all booked, or the nightly rates were way too high. We were only paying $60 per night at Royal Court Apartments, and we sure liked that rate, especially since we had to pay for 14 nights of lodging.
We tried to find the good things about Royal Court, and acknowledged that the price was right, the air conditioning was cold, the WiFi signal was strong, we had our own kitchenette, and we were close to the boatyard. We came up with a plan to make this place work. For just $50, we could go to ACE Hardware, buy some spray foam to plug the hole in the bathroom, get a full length mirror, and fix the toilet stopper. I swept and re-cleaned the floors since it wasn’t done well before we got there, wiped down the counters, bathrooms, etc., and brought some items from our boat to make it more homey for the next two weeks. After that, we never had another cockroach come through the wall, and the cleanliness made it more tolerable. After discussing a few of the issues with the owners, the agreed to reimburse us for the items we purchased, and apologized profusely. Come to find out that this is an unfinished room, and they didn’t have space to put us in one of their finished apartments. It all made sense and we became friends with Chevonne and her husband.
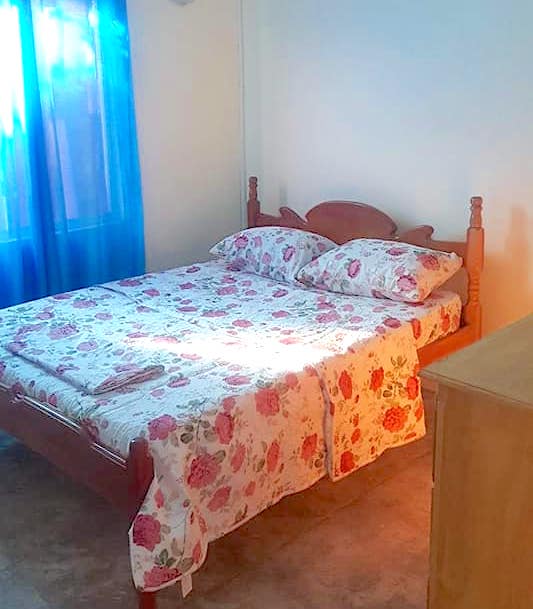
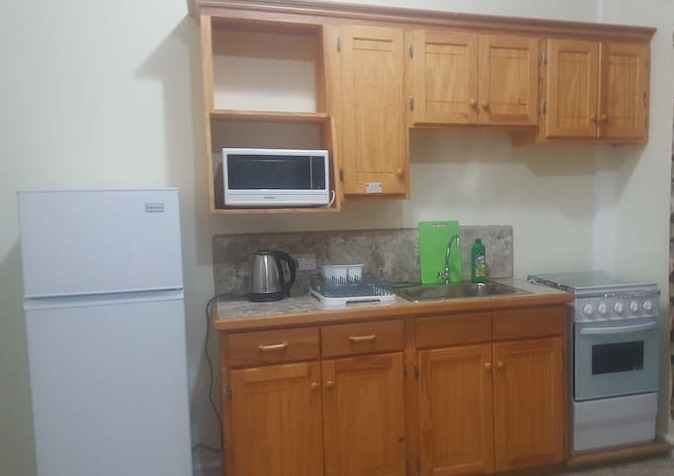
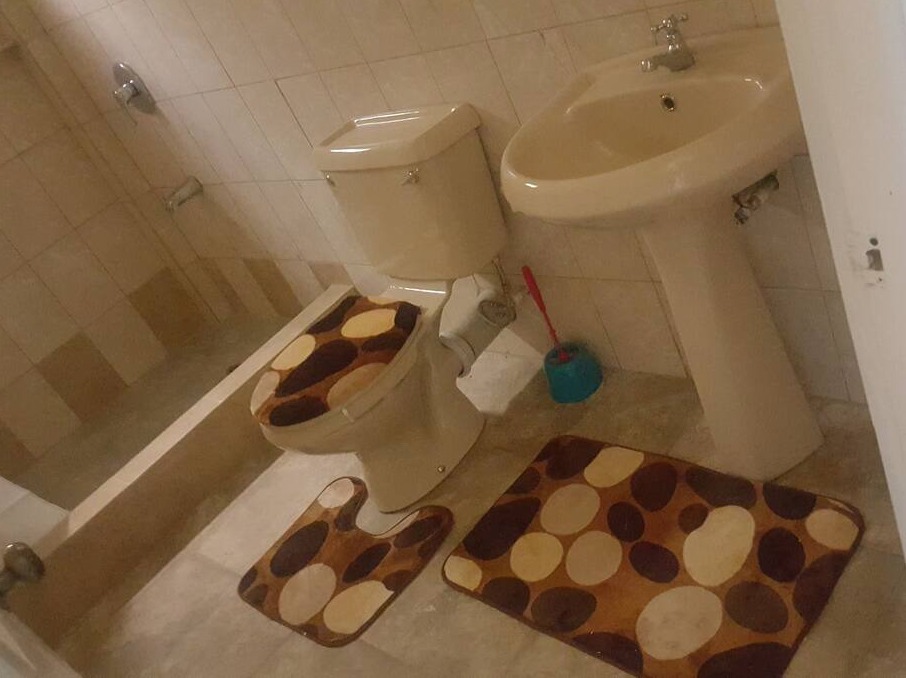
We were so glad we chose to stay at Royal Court because being near the boat turned out to be the best decision we could have made. The funny thing is, this little apartment grew on us, and it certainly made us even more grateful when we returned to the comforts on our boat. For those getting work done at Clark’s Court, I would recommend this place for its convenience, price, and cold air conditioning. Just don’t expect it to be “royal.”
Back to the boat! When we first had the boat hauled out, hanging in the slings on the boat lift, workers began power washing the hull. It had a lot of growth on it, but not nearly as much as we had expected. The bad news was that the bottom paint was peeling down to the hull, and it was quickly determined that we would need to have the paint removed, start over with a new primer, then two coats of bottom paint, and a third coat along the leading edges. This, of course, added to the cost, but thankfully, Linden, the owner of Fiber Tec Yacht Services, the company doing the job, said he could get all the work done in the two-week timeframe. He had his men start the job right away, and within the first week, the boat paint was stripped, sanded, primed, and painted. FiberTec did a great job with the painting.
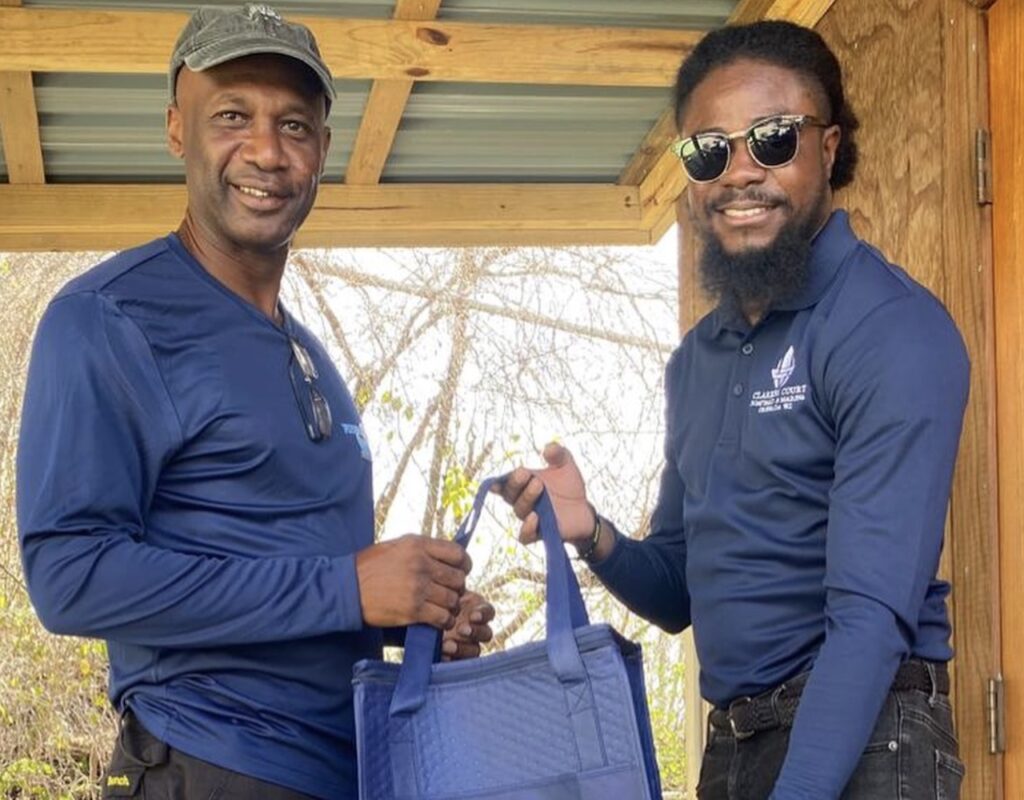
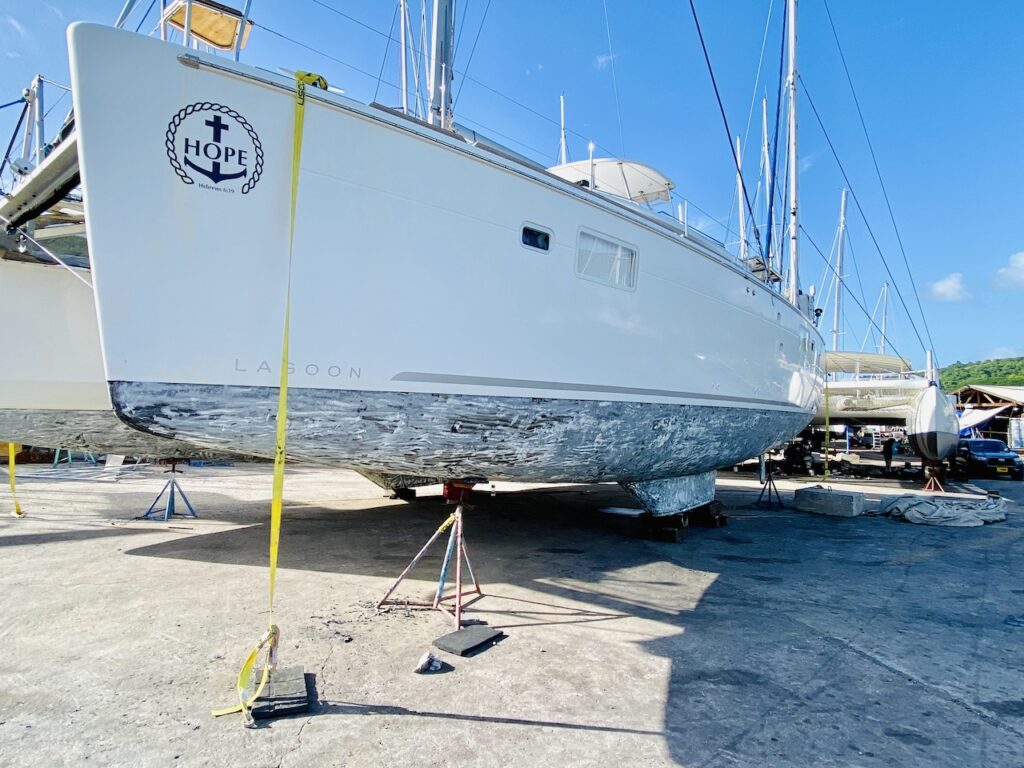
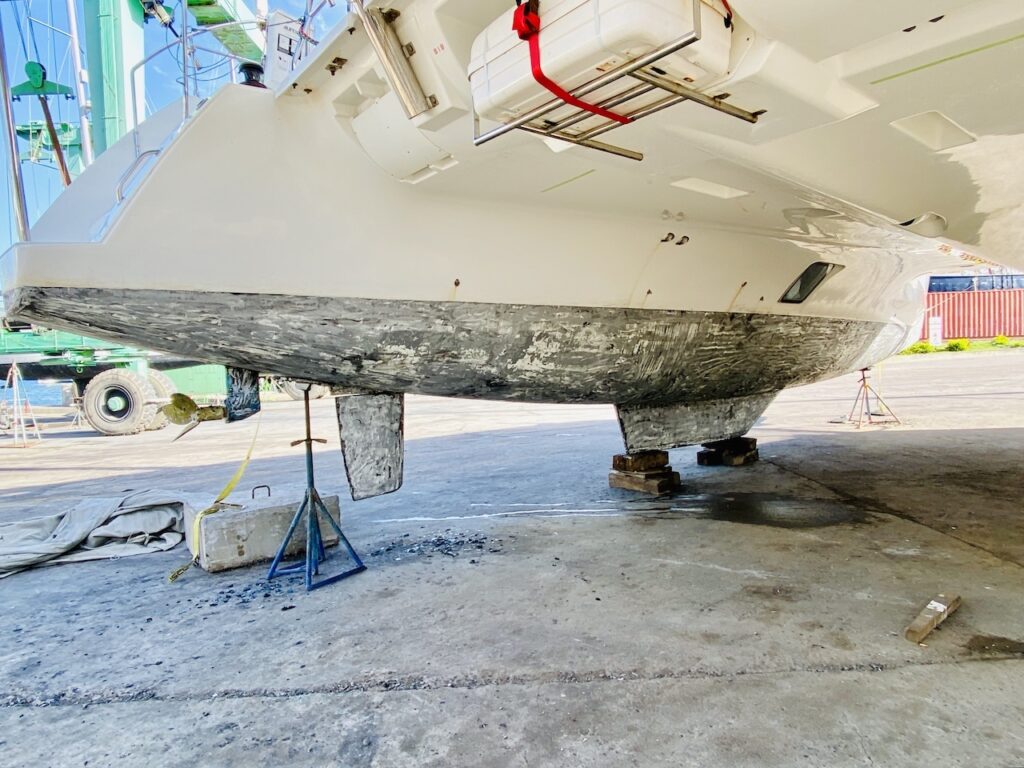
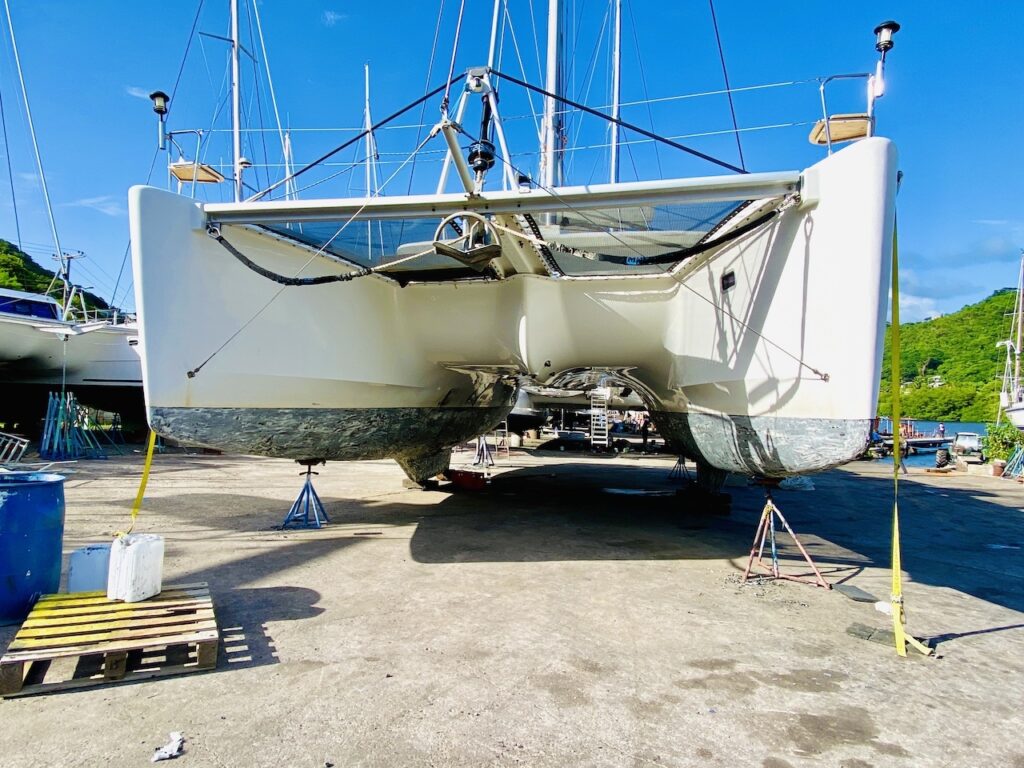
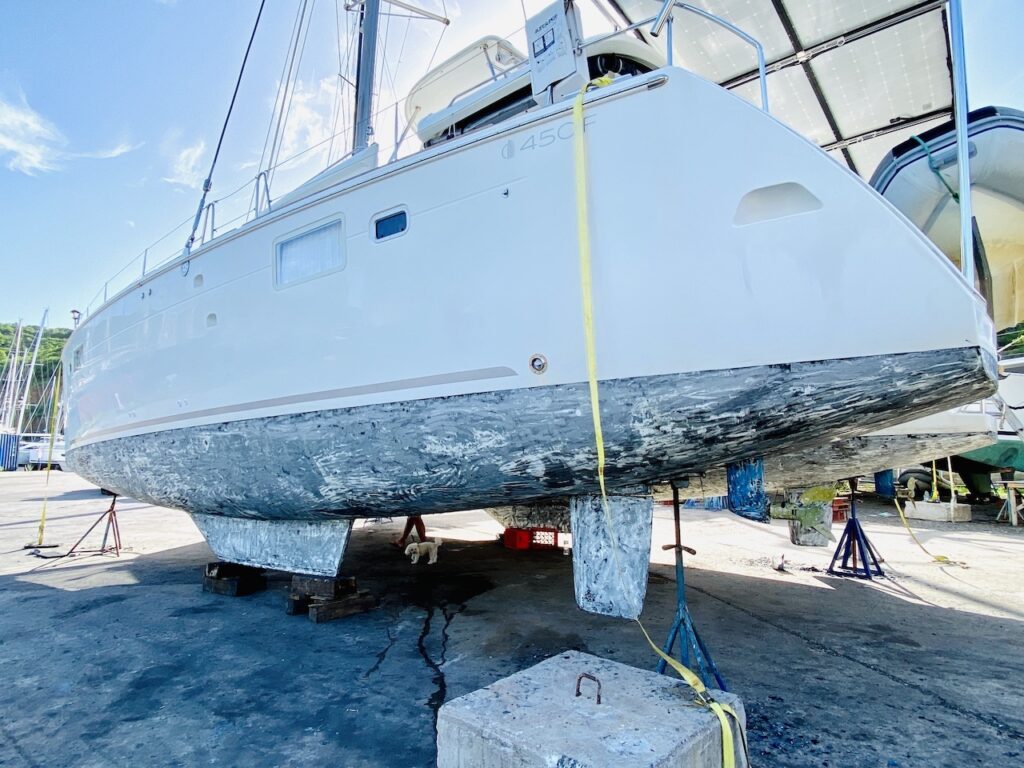
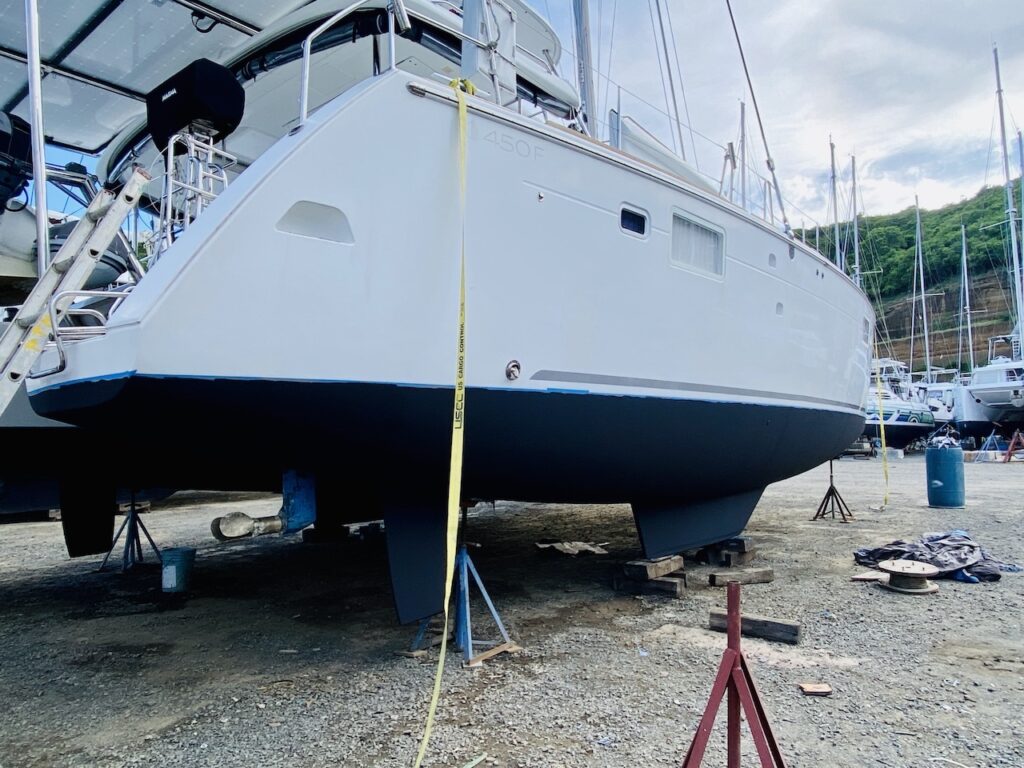
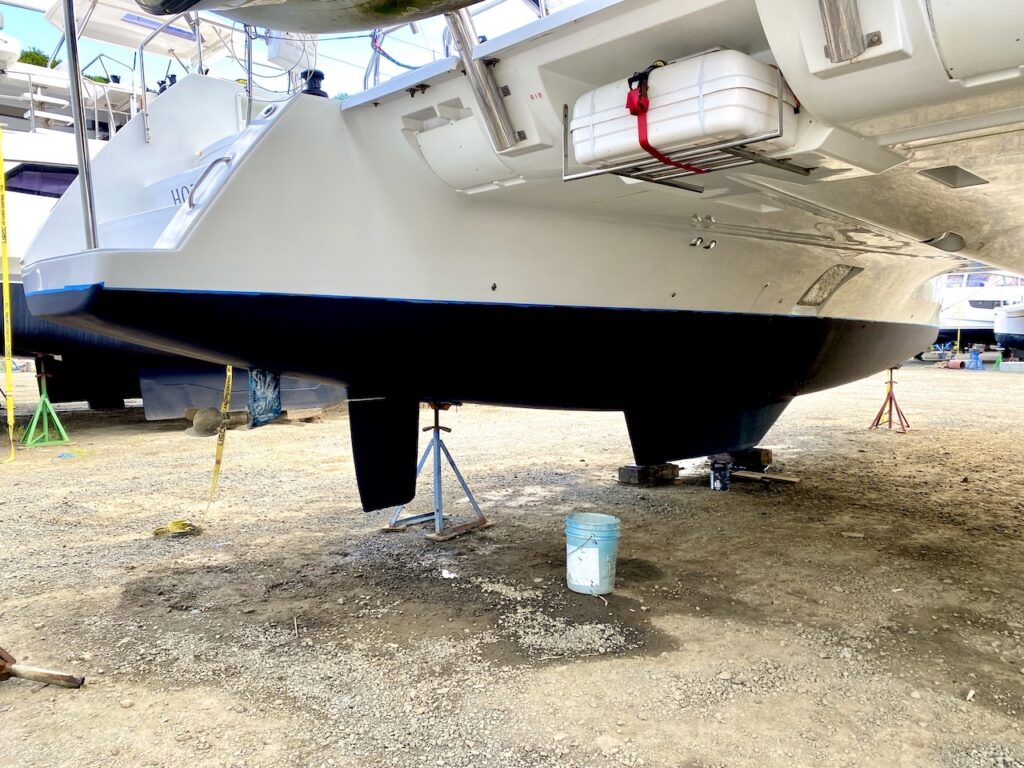
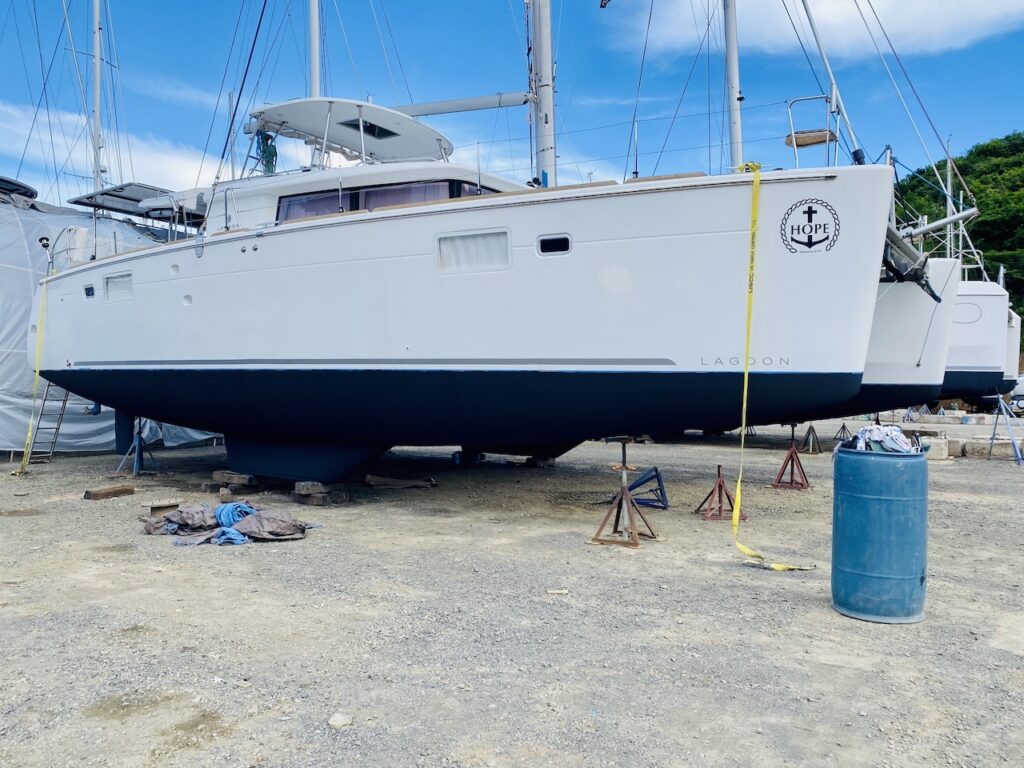
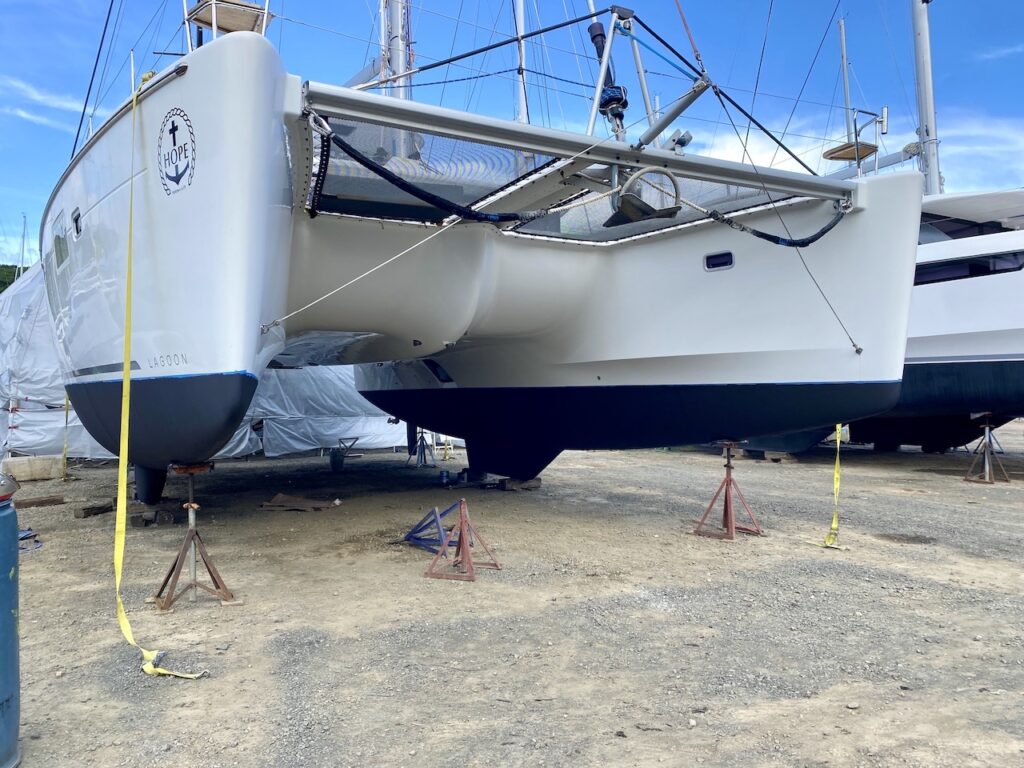
For those interested, we used five gallons of Sea Hawk Biocop TF Dual Biocide Antifouling Bottom Paint. This was what was originally on the hull when we purchased it. When we hauled out in Matthews, Virginia, last summer, Zimmerman Marine put one coat of a different paint on top of the original Biocop, and it just didn’t bond properly because the paints were chemically dissimilar. Now that we started the paint process from scratch, using top quality paint, we most likely won’t need to repaint for another two years.
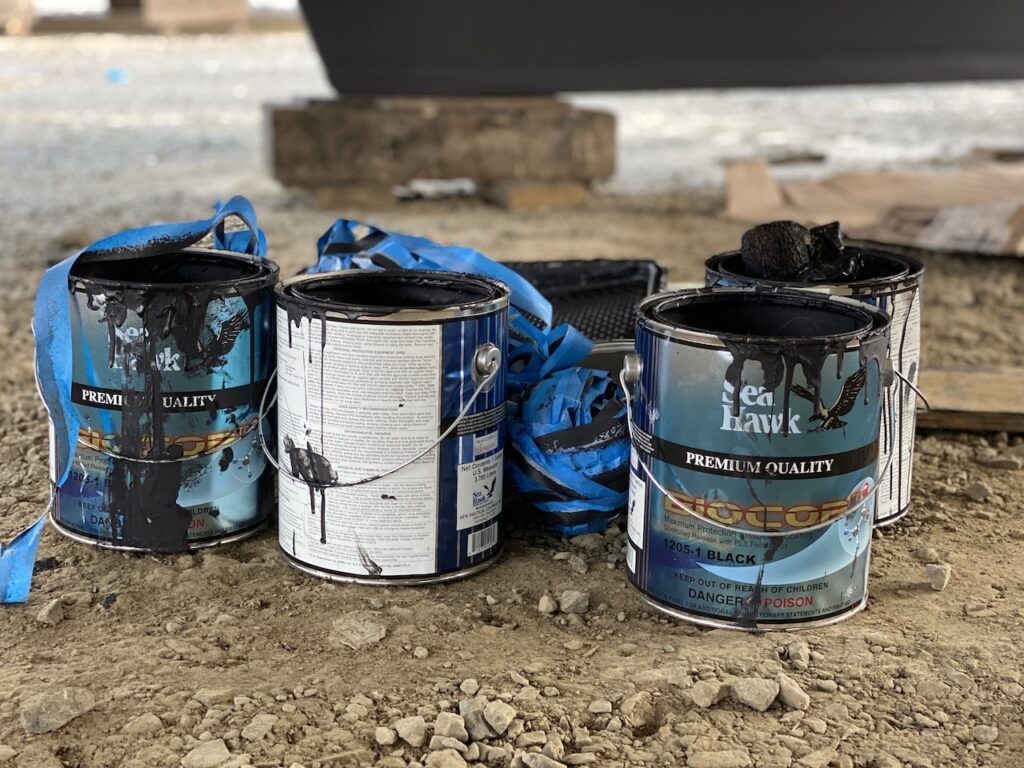
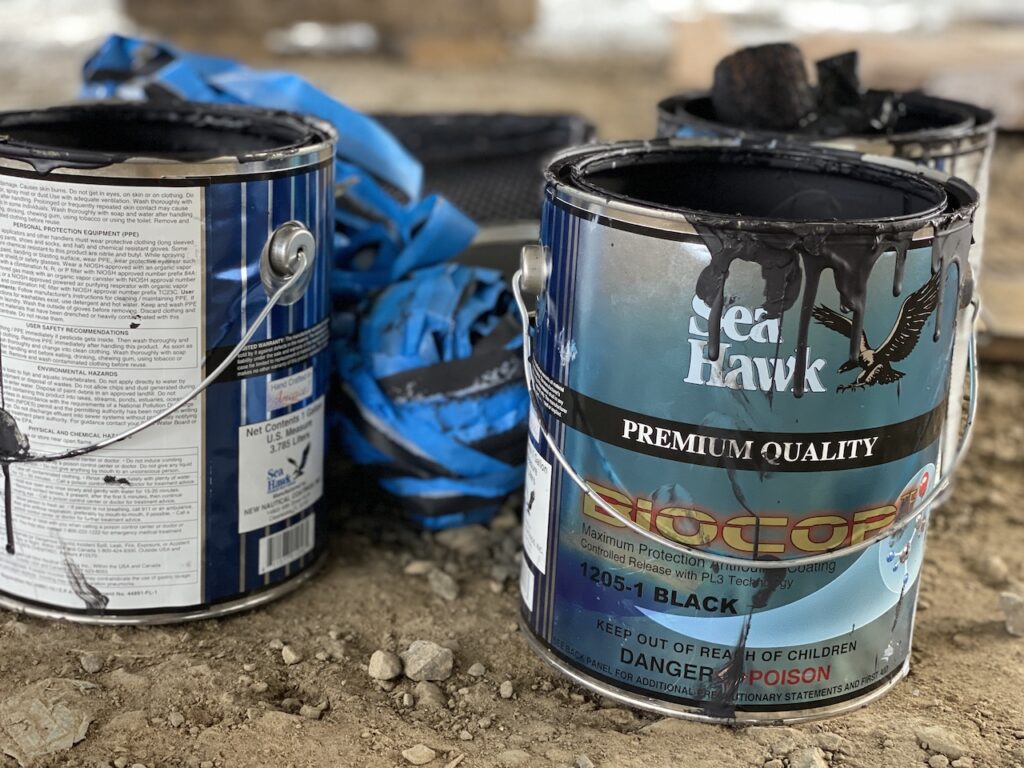
In addition to the painting, we had the sail drives serviced. This job involved changing the sail drive oil, replacing the seals, checking the diaphragm, sanding the prop blades, painting the props with a corrosion and copper-free antifouling paint, and installing new zinc anodes. Nichol is the expert on this job, but he was sick the first week we hauled out. FiberTec put another worker on the job who wasn’t schooled in what was required for a sail drive service. This is one of the reasons we were so glad to be near the boat, as Kory was able to stop the job from being done incorrectly. The owner held off on its completion until Nichol was well and could do the job correctly. And that he did! It’s too bad I didn’t get an “after” picture of the shiny props, new zincs, and freshly painted sail drives.
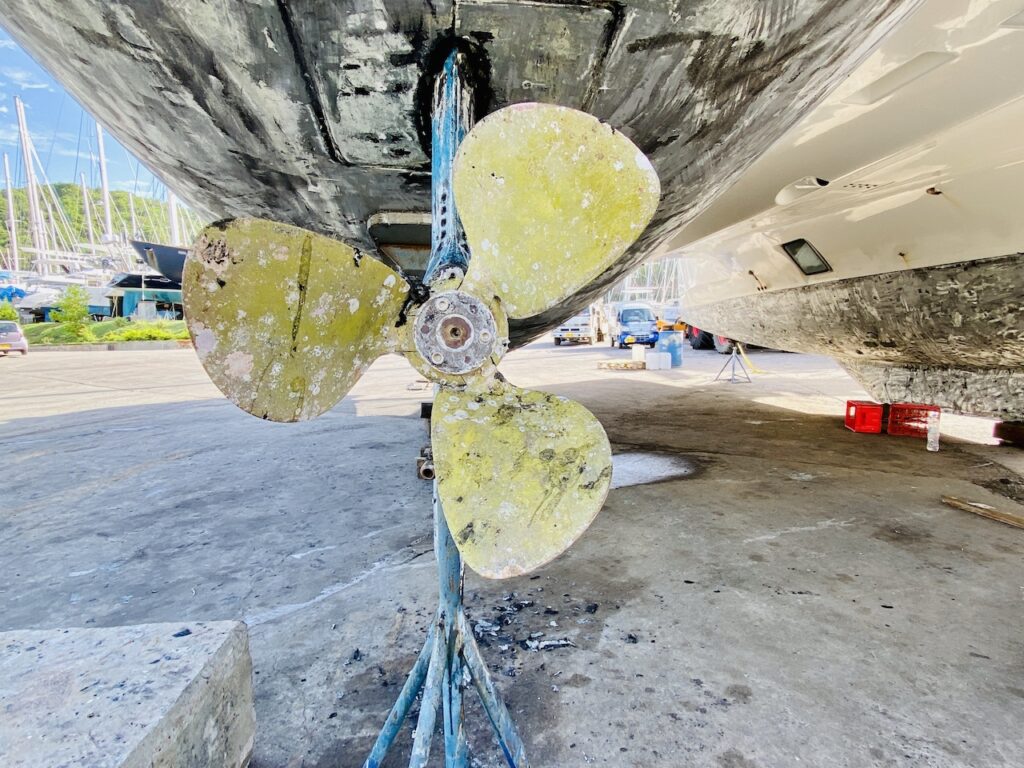
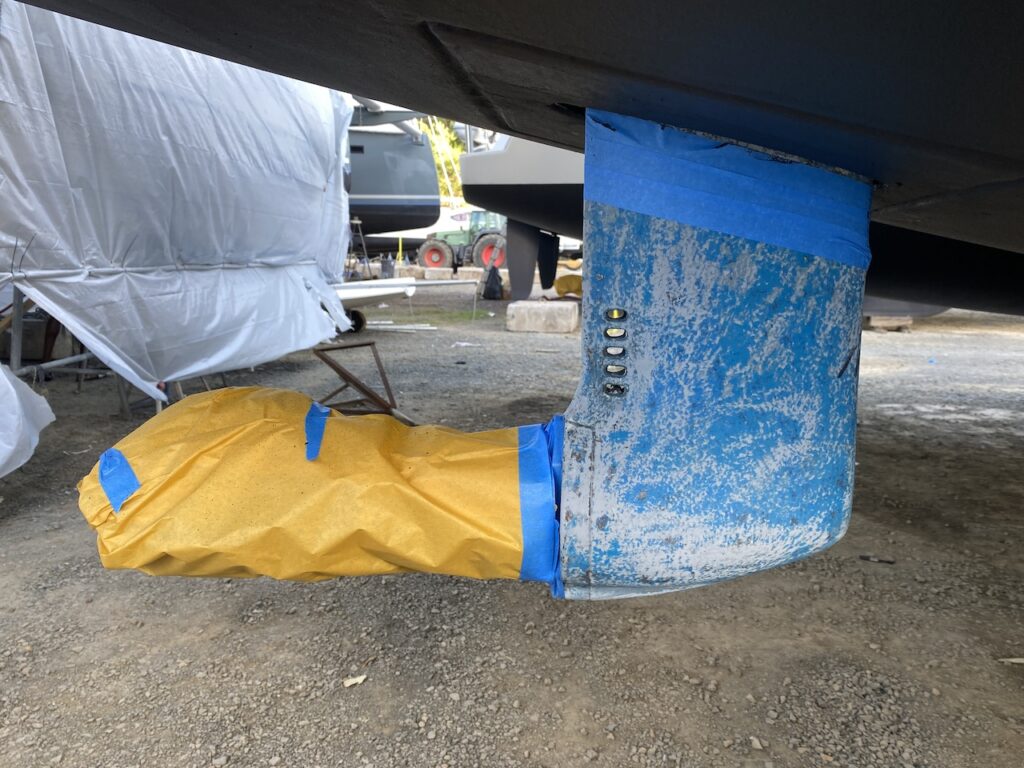
Kory and I did some work ourselves while the boat was hauled out. He changed the hull zincs, lowered the dinghy and did a full service and oil change of the motor. I spent time doing detailed cleaning of appliances, counters, and cupboards, and organizing our food storage and supplies.
Part of our service contract with FiberTec included an acid wash of the entire boat. Acid washing removes discoloration such as yellowing, rust, dirt, and hard water spots on both flat and non-skid surfaces. Once the muriatic acid and water solution is mixed, it is sprayed on the boat, allowed to sit, brushed, and then rinsed off. For the most part, this brightened our boat right up and made it look new again. However, we ran into quite a few problems. The workers sprayed the acid wash on the stainless steel surfaces, where it wasn’t supposed to be applied, and they failed to wash it off thoroughly. The next day, we had muriatic acid stains all over the boat, with tarnished and spotted stainless everywhere. We called Landon to the boat to inspect it, and he agreed that the acid washing job was not done correctly. This error caused hours of extra work for his employees as they had to clean all of the stainless latches, poles, stanchions, and metal surfaces. We weren’t charged for this extra work, and Landon even threw in a full stainless polish free of charge to compensate for the error. There are a few acid stains remaining that could not remove, but there wasn’t much we could do about it. We just hope FiberTec chalks this up to a learning exercise and does the job correctly next time. Miguel was a hard worker who helped rectify the problem and made sure we were happy with the finished cleaning of the boat.
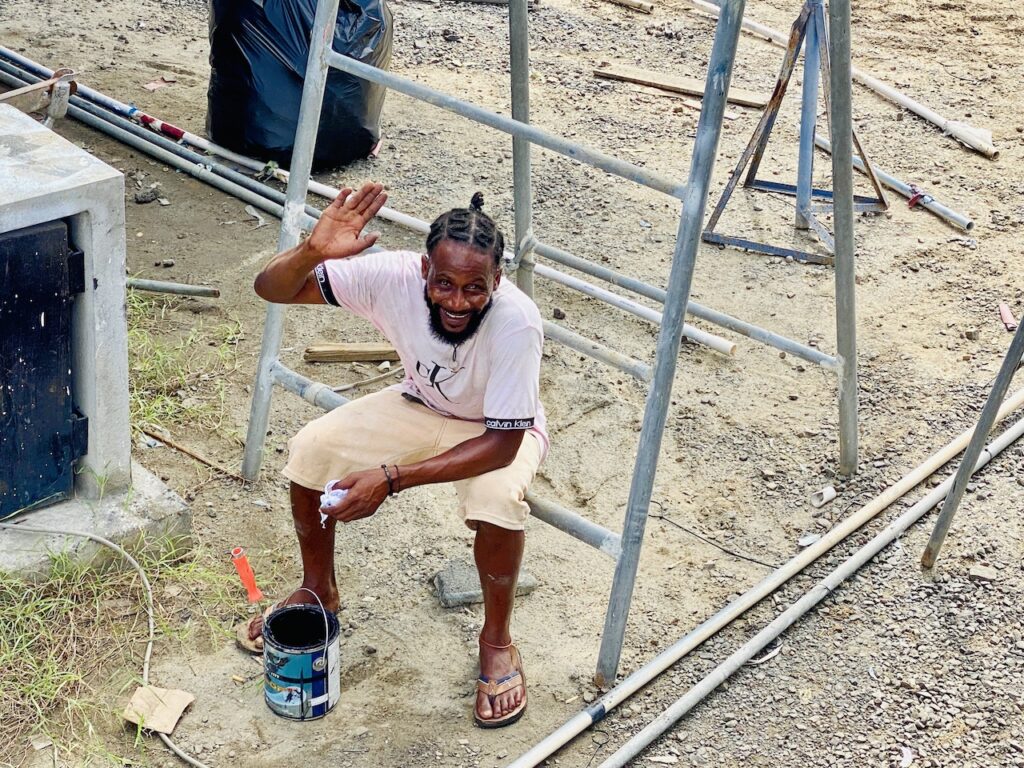
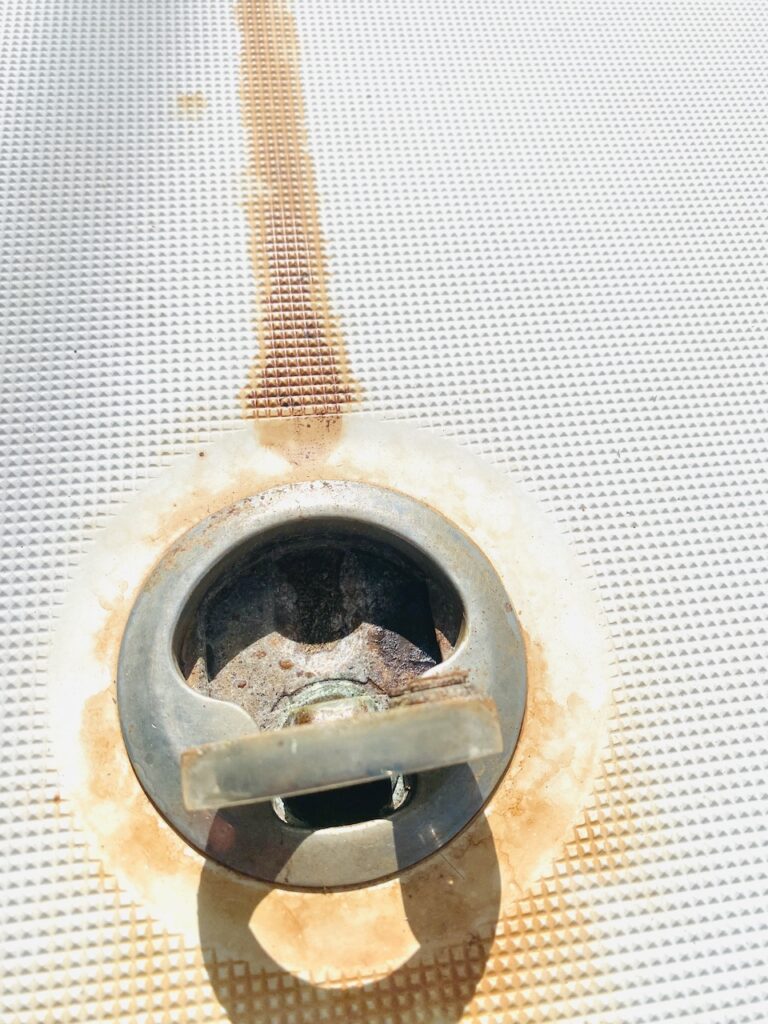
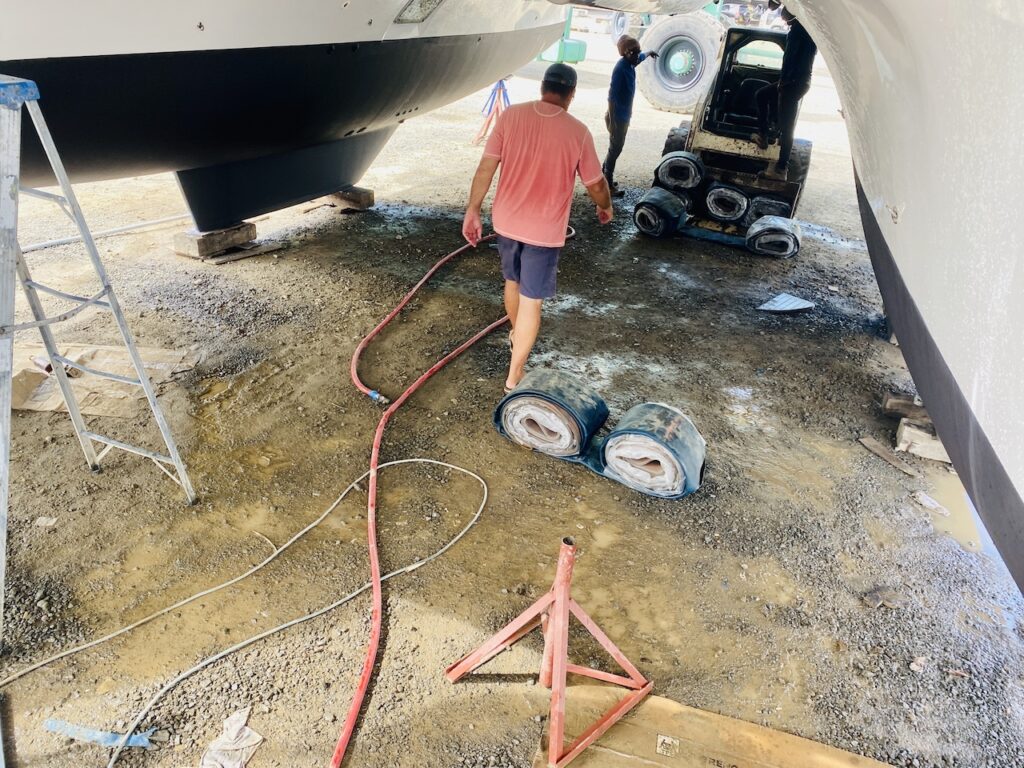
October 22, 2024 was our scheduled day to hoist the boat and get it back in the water. Cruisers call it “Splash Day!” All the work was done, down to the wire, and we were able to splash. That morning was busy though. The workers did a final rinse of the boat and finished cleaning the stainless, while I used a chamois brush to dry the surfaces and started putting the outside cushions back. Kory took the rags out of the through holes that had been stuffed there to keep dust and critters out. We hung fenders on both sides of the hulls and looped dock lines around the cleats at the bow and stern of the boat, and were prepared to get the boat lifted into the slings. I stayed on the boat with Gracie to experience the process, and Kory stayed down below to make sure everything was done correctly.
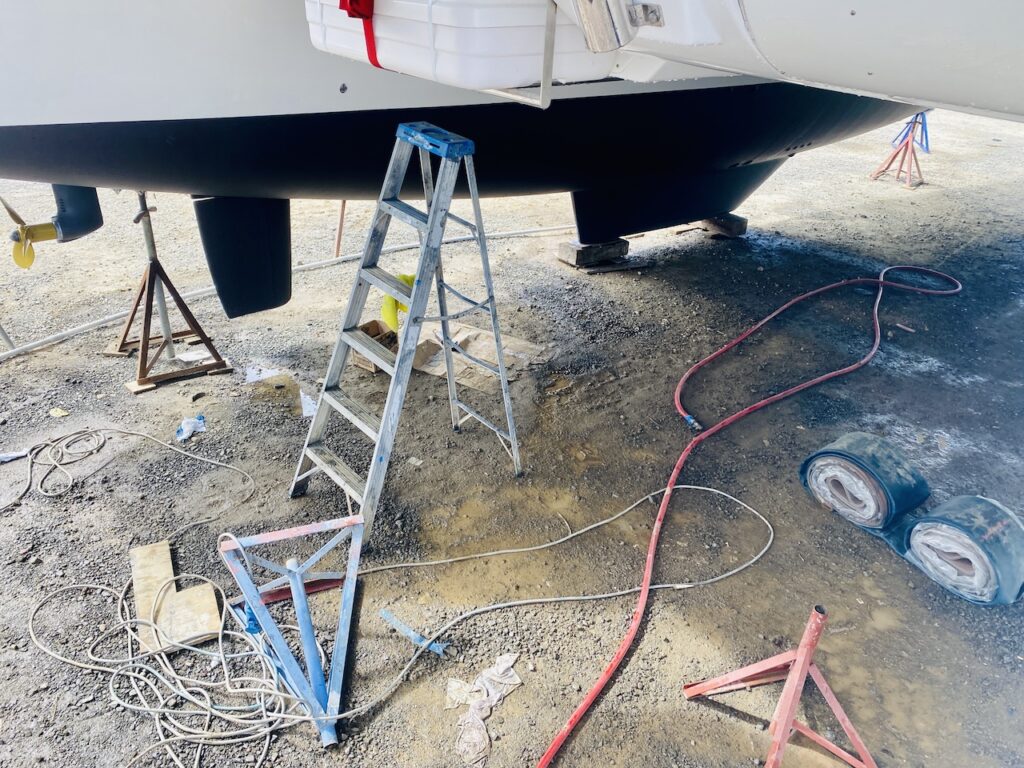
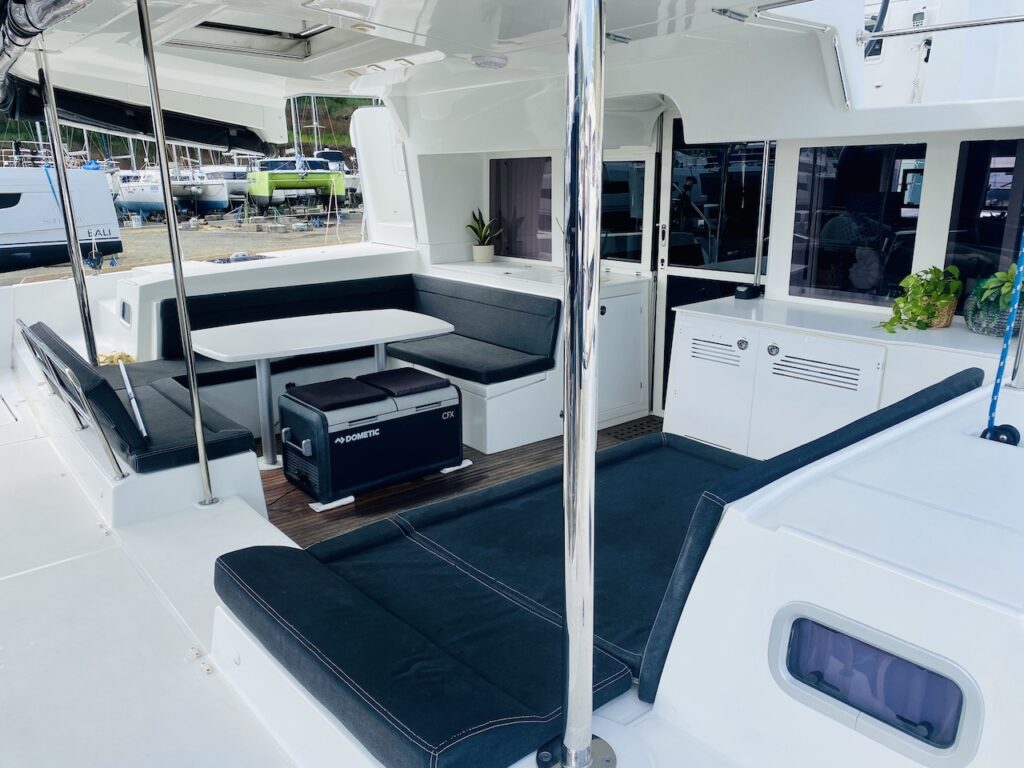
Once the lift hoisted the boat off the blocks, workers painted a coat of the Seahawk Biocop anti-fouling paint to the places where the bottom had been resting on blocks and supports. They let this dry for a short time before moving the boat.
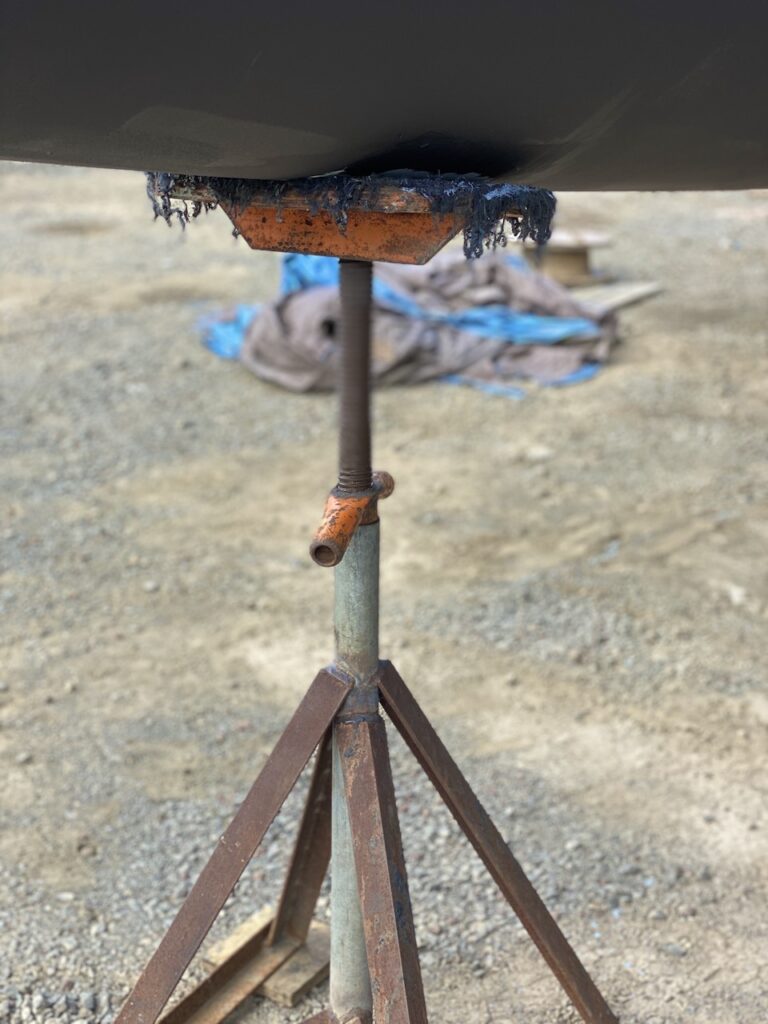
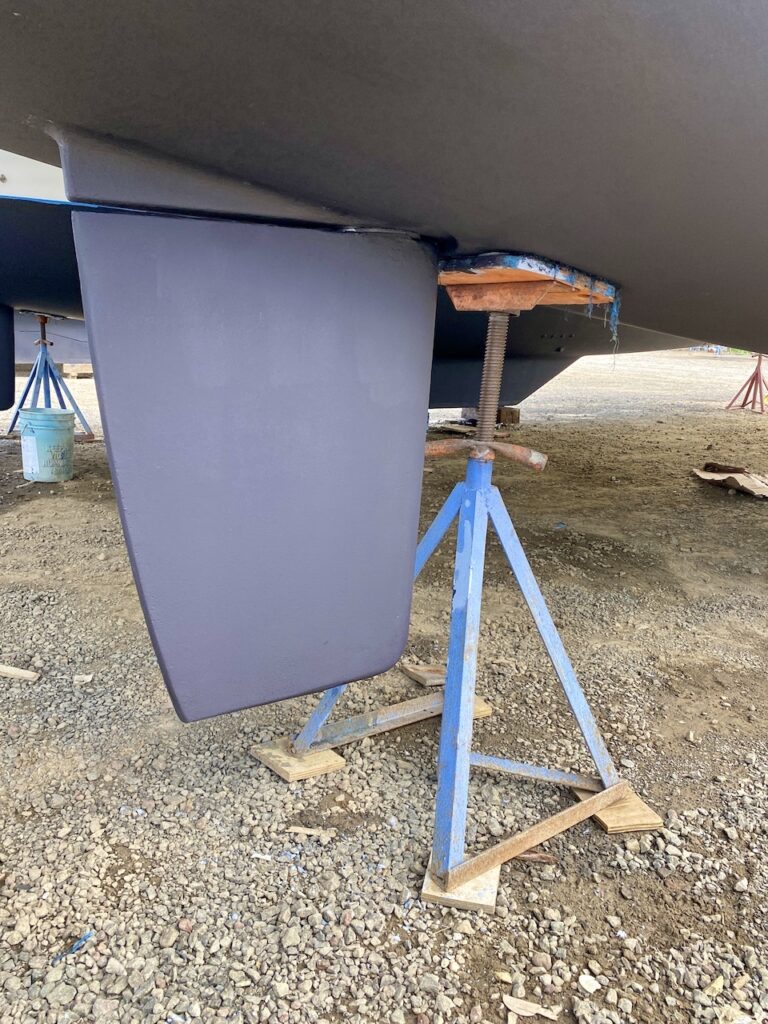
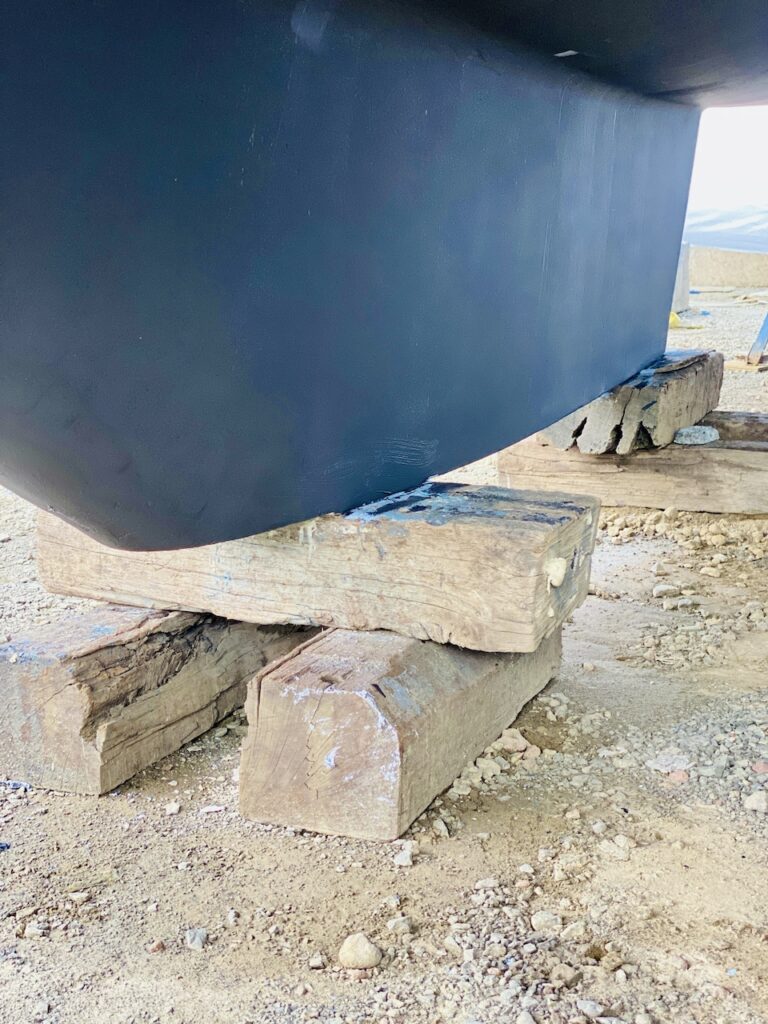
It was an odd experience sitting inside the salon as Hope was hoisted onto the boat lift. I initially heard some cracking sounds as the full weight of the boat settled into the slings, then it was a quiet, smooth ride as the boat was driven remotely to the boat ramp. The workers at Clark’s Court Marina expertly lowered Hope into the water, and Gracie started to get really excited. I think she knew we would be on the move again.
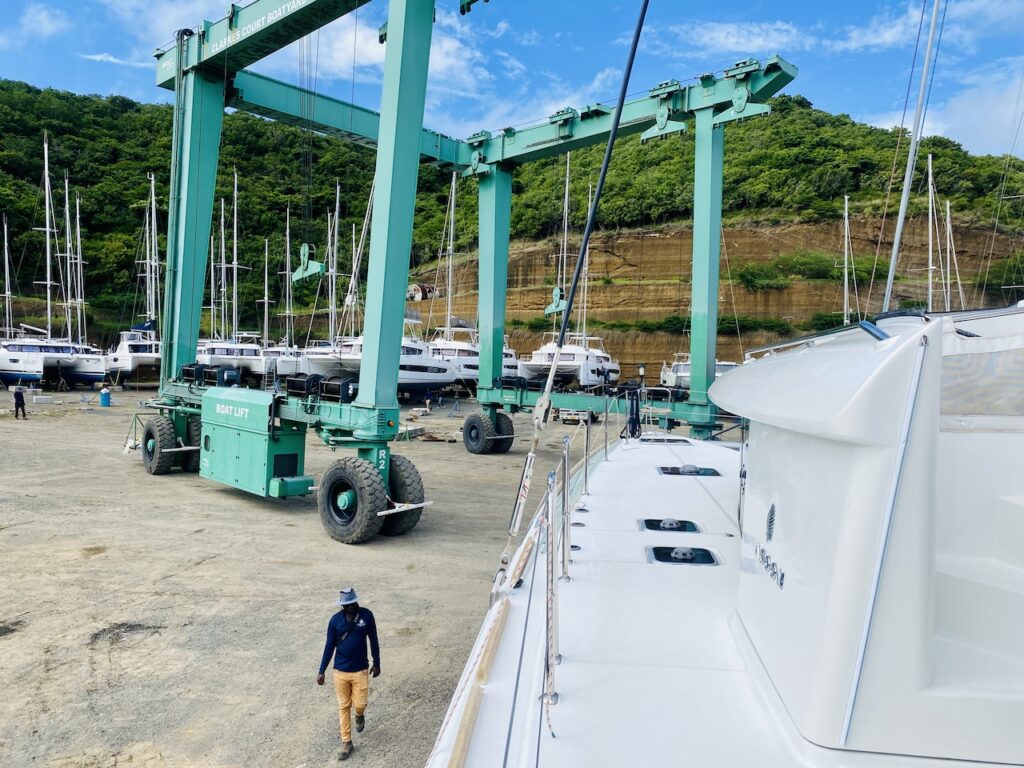
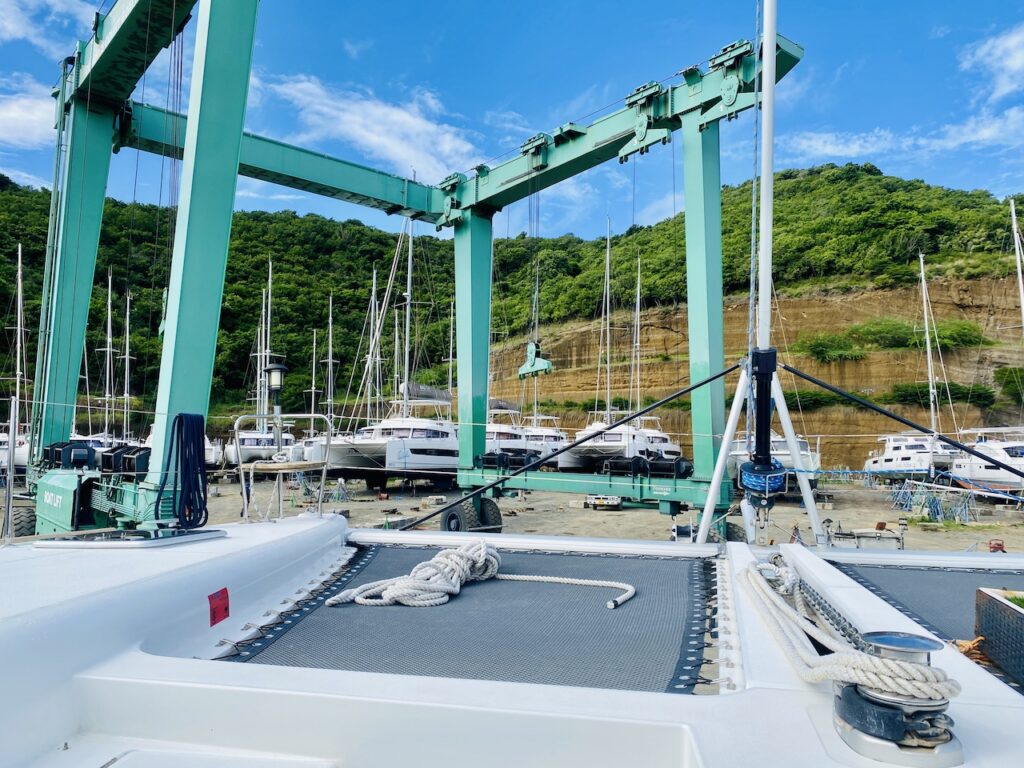
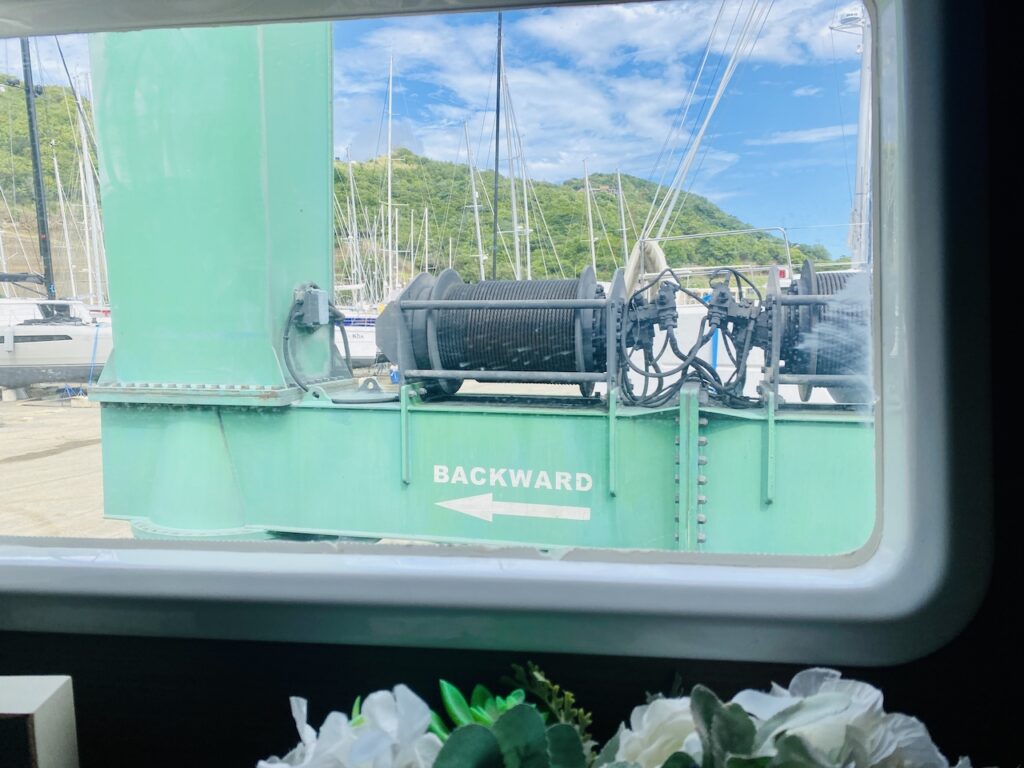
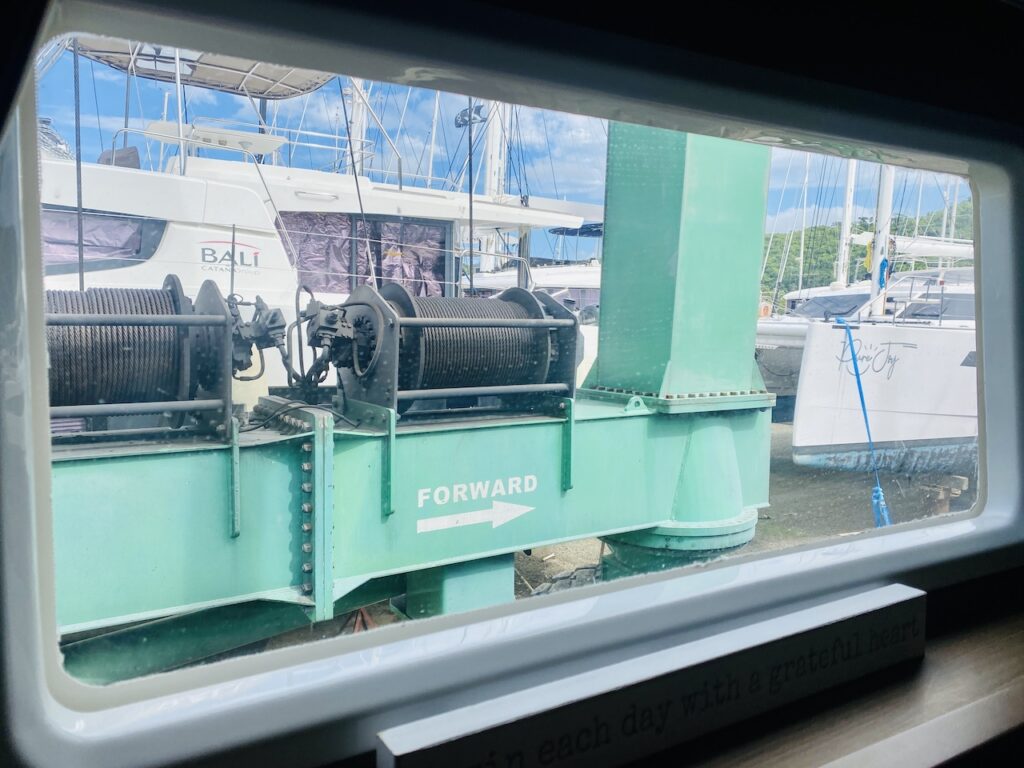
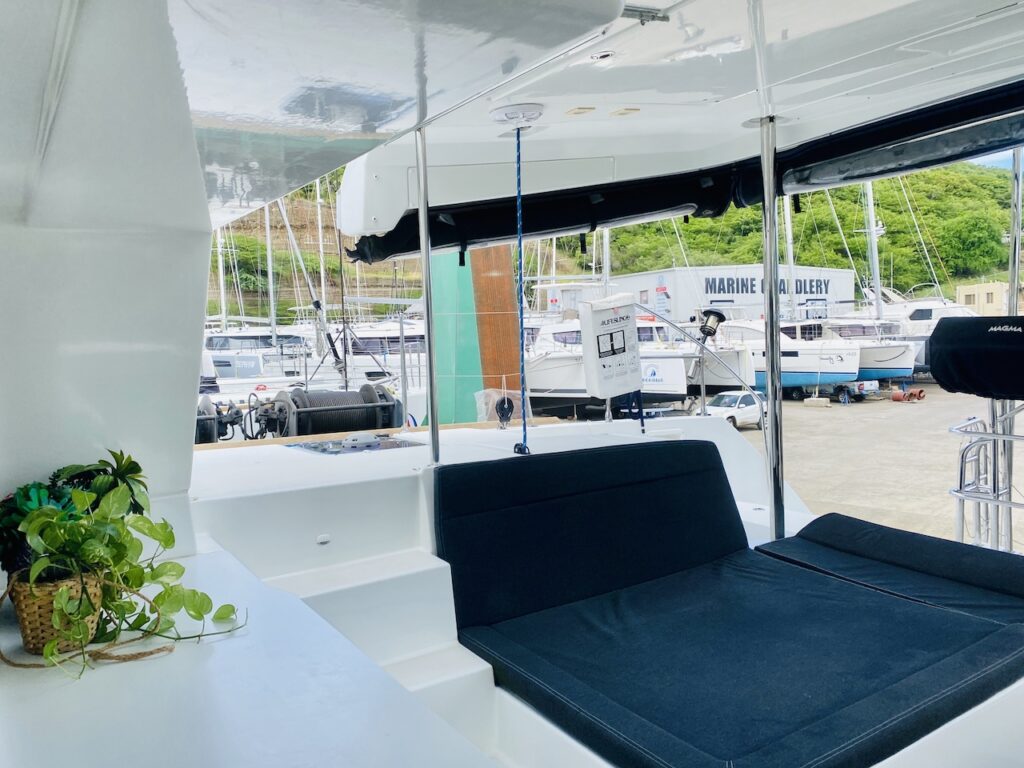
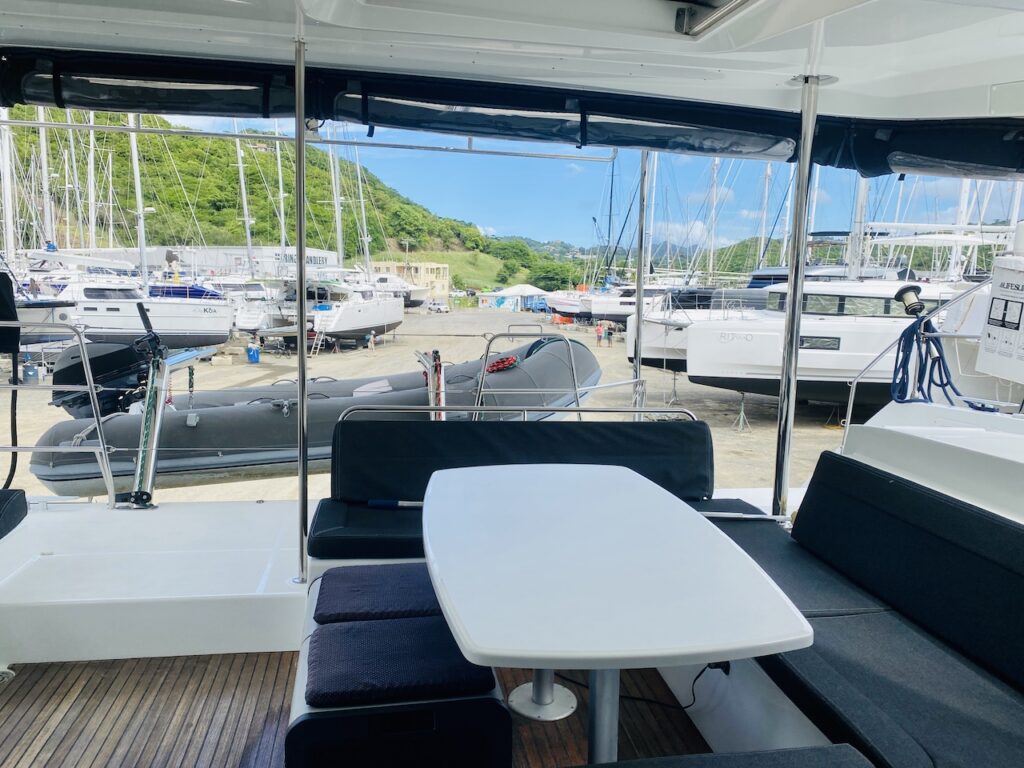
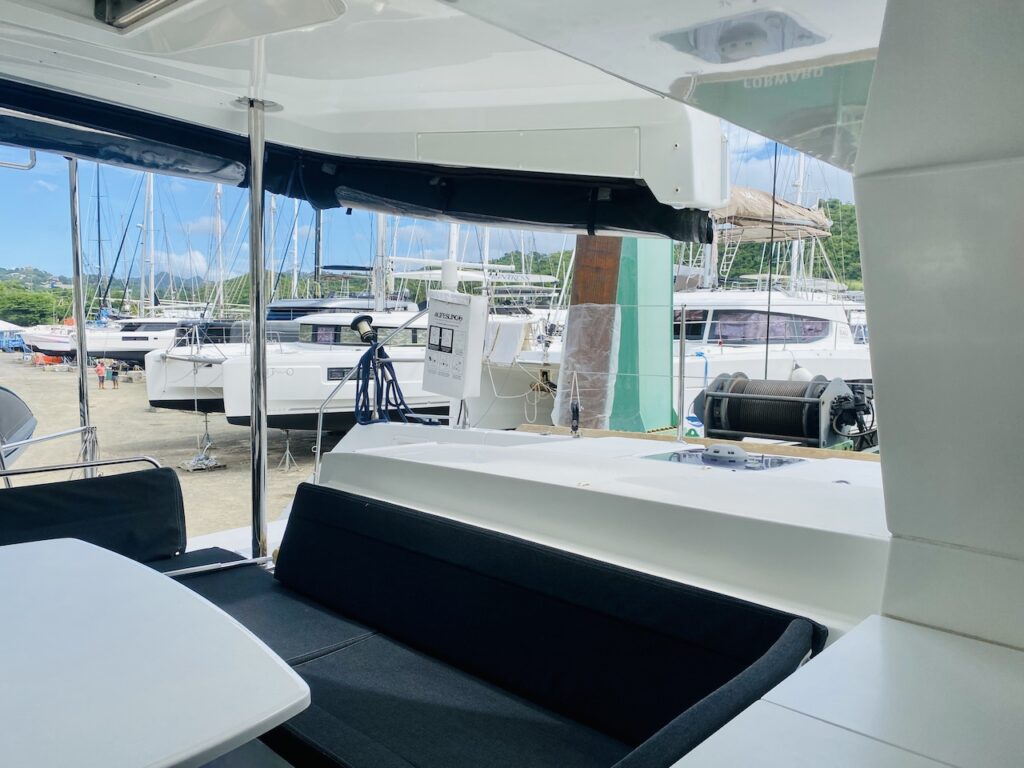
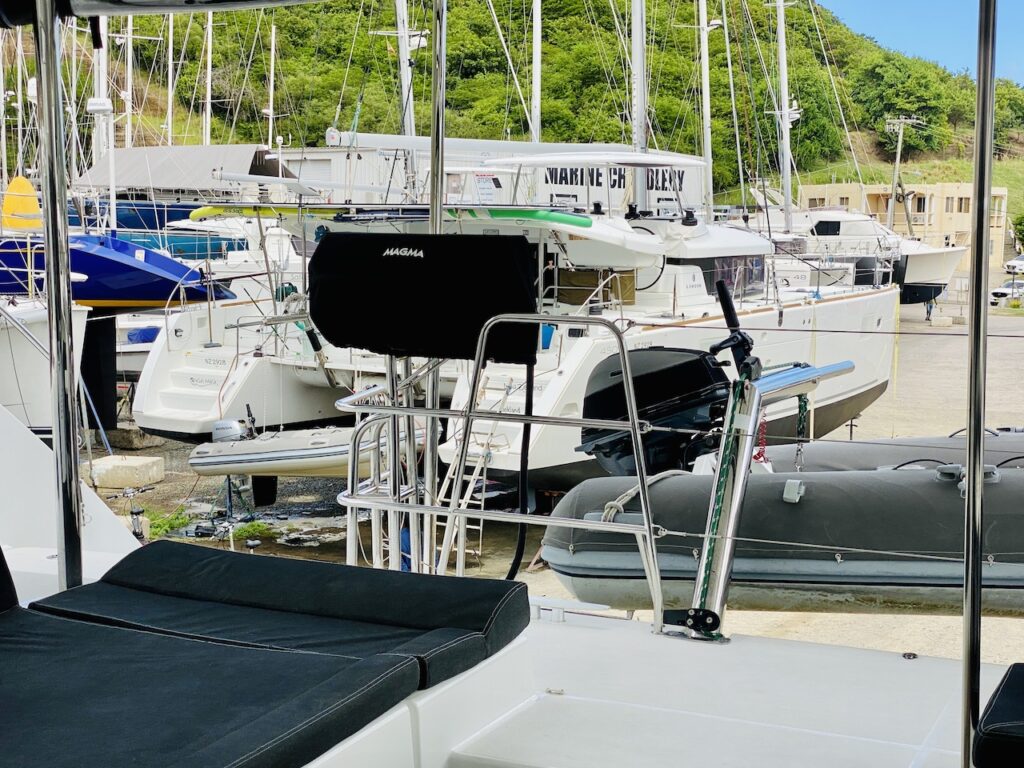
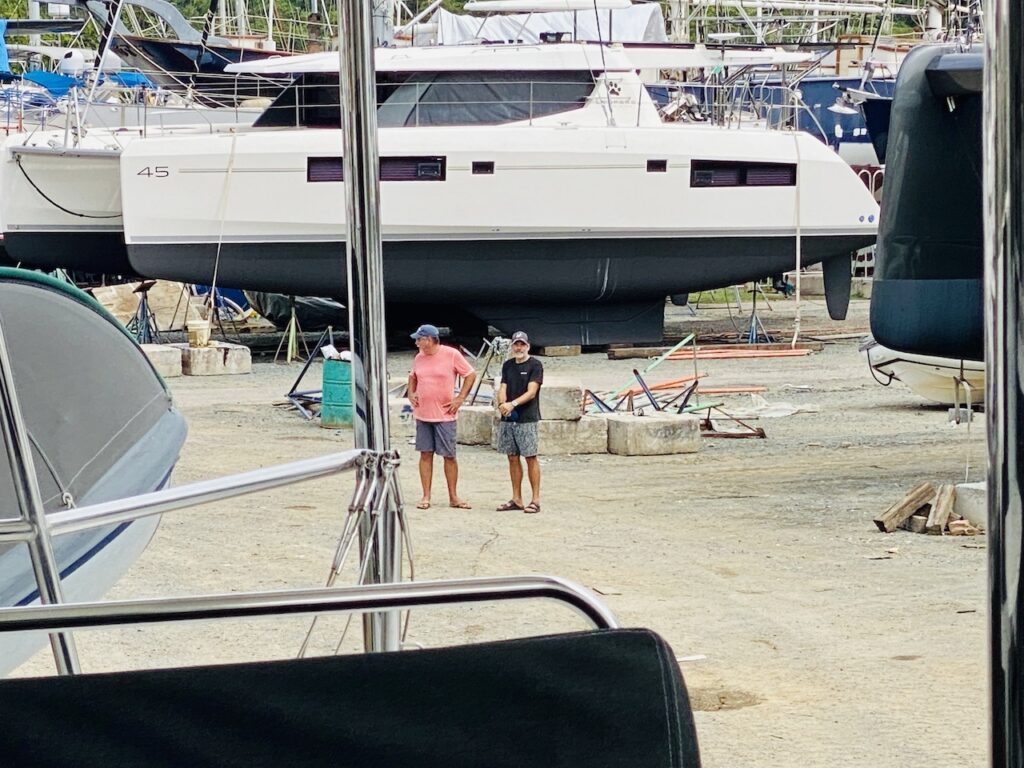
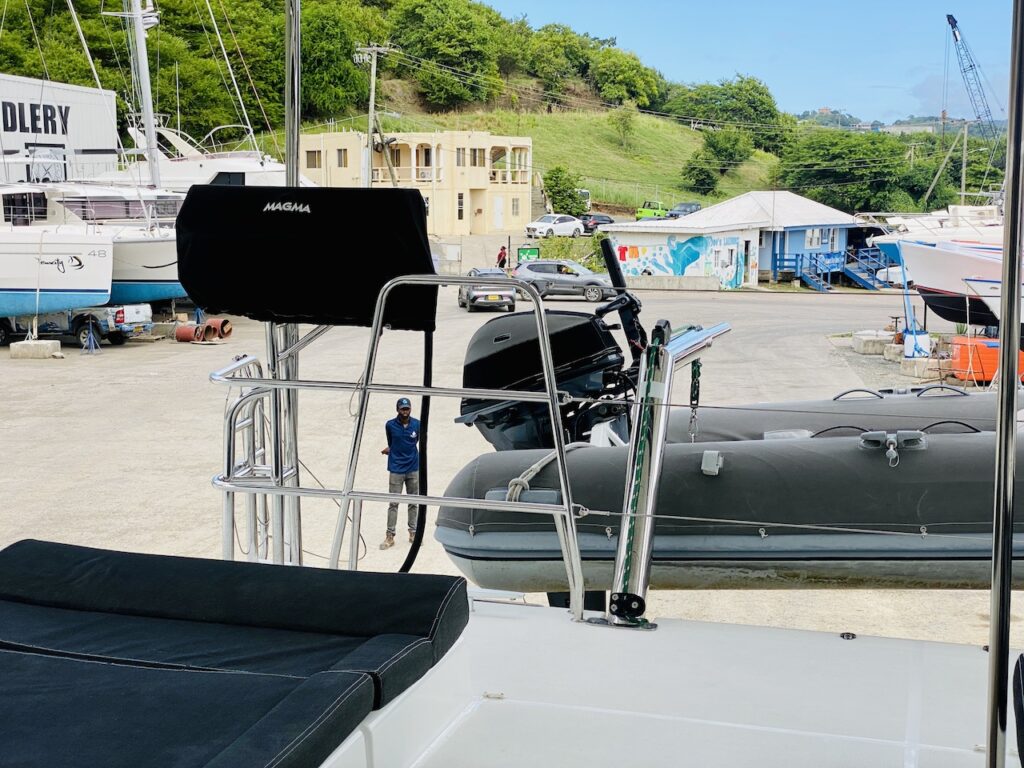
Once in the water, we had to tie the boat to the dock at the stern and the bow, while Kory and I started the engines, checked the exhaust, and inspected the bilges to make sure none of our through-holes had leaked. All was working well and we were ready to leave. It was a windy morning, but Kory did a great job backing up the boat and getting us out into the bay. I took off the fenders and dock lines while he captained the boat and brought us back to Spice Island Marina in Prickly Bay where we would have our mainsail and Genoa reinstalled the following day. That process went well, and the haul-out was complete.
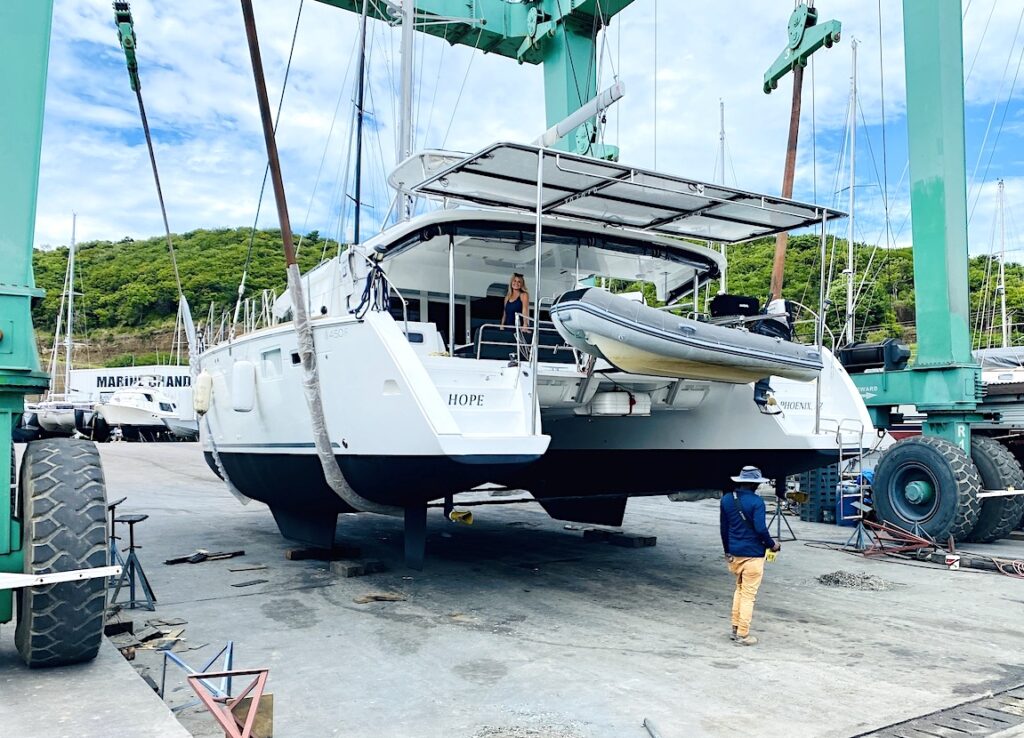
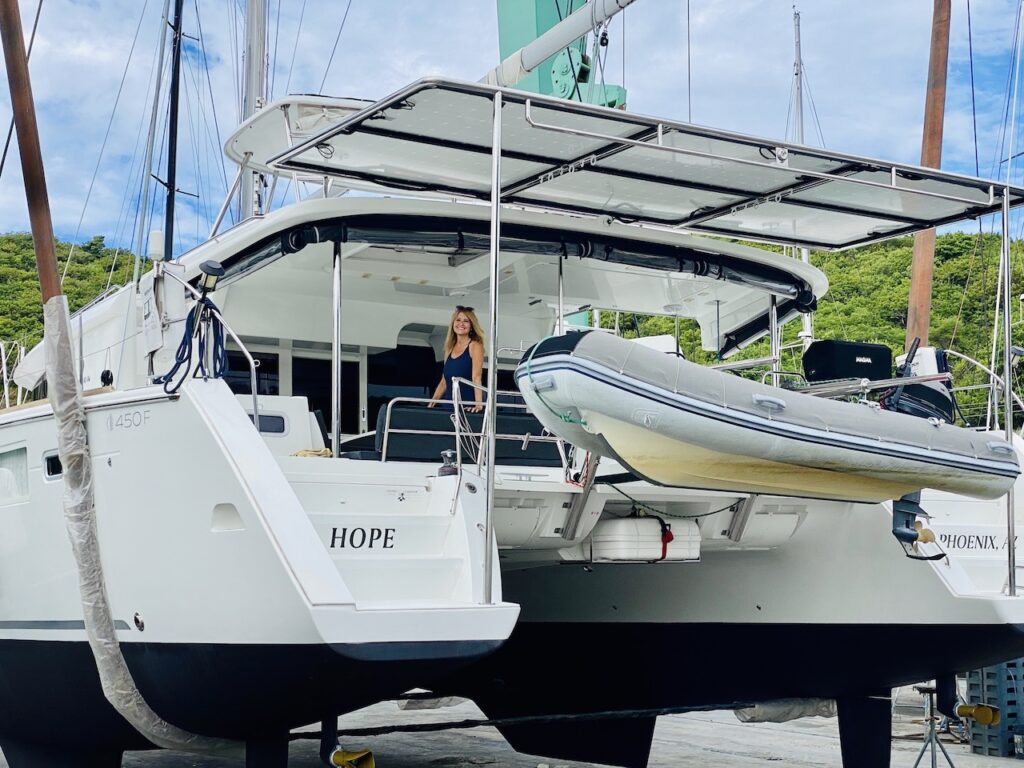
Hope looks great with her thorough cleaning and waxing, fresh bottom paint, shiny stainless, smooth props, dust-free cushions, and everything put back in order. It’s time to take her for a sail and let the wind glide us through the beautiful Caribbean waters! Smooth sailing, here we come!